
Rio Tinto Iron Ore Heavy Haul Railway Maintenance
Client: Rio Tinto
Location: Pilbara, WA, Australia
Business Segment: Urban Solutions
Industries: Mining & MetalsInfrastructure
Services: Maintenance

Executive Summary
Western Australia's Pilbara region is an unforgiving and surprising place. Temperatures can soar above 110 °F under a blazing sun and plunge below freezing at night. The arid, rust-red landscape rarely receives rainfall; when it does, dry ravines can suddenly fill with roiling waters brought by seasonal typhoons. Snakebites and dehydration are ever-present dangers. Below the rocky surface of this inhospitable land, however, lie vast deposits of iron ore, a valuable resource that is being excavated from 14 mines, loaded onto rail cars and transported to three separate shipping ports hundreds of miles away.
Since 1968, Fluor has been providing track maintenance, construction and replacement and maintenance of track machines for Rio Tinto Iron Ore's heavy haul railway. It is a task in a terrain filled with complex challenges, just the kind of conditions in which Fluor performs best.
Client's Challenge
Below the rocky surface of this remote location lies a vast deposit of iron ore, a valuable resource that is being excavated from eleven mines, loaded onto rail cars and transported to two separate shipping ports hundreds of miles away. In addition, the ore must travel to those ports on railways constantly degrading under the massive weight of trains about two kilometers and 230 cars long.
Rio Tinto's Iron Ore Heavy Haul Railway is the largest privately owned rail structure in Australia and one of the largest heavy-tonnage railways in the world.
On its more than 1,400 kilometers of track, Rio Tinto transports ore from its mines at Tom Price, Paraburdoo, Brockman, Hope Downs, West Angeles, Robe Valley, Yandicoogina and Marandoo to ports at Dampier and Cape Lambert.
Rail maintenance was only part of Rio Tinto's overall plan for the railway system. The company needed a partner to continually address its needs for additional track and provide oversight for the array of Rio Tinto's machinery used to build and maintain the railway.
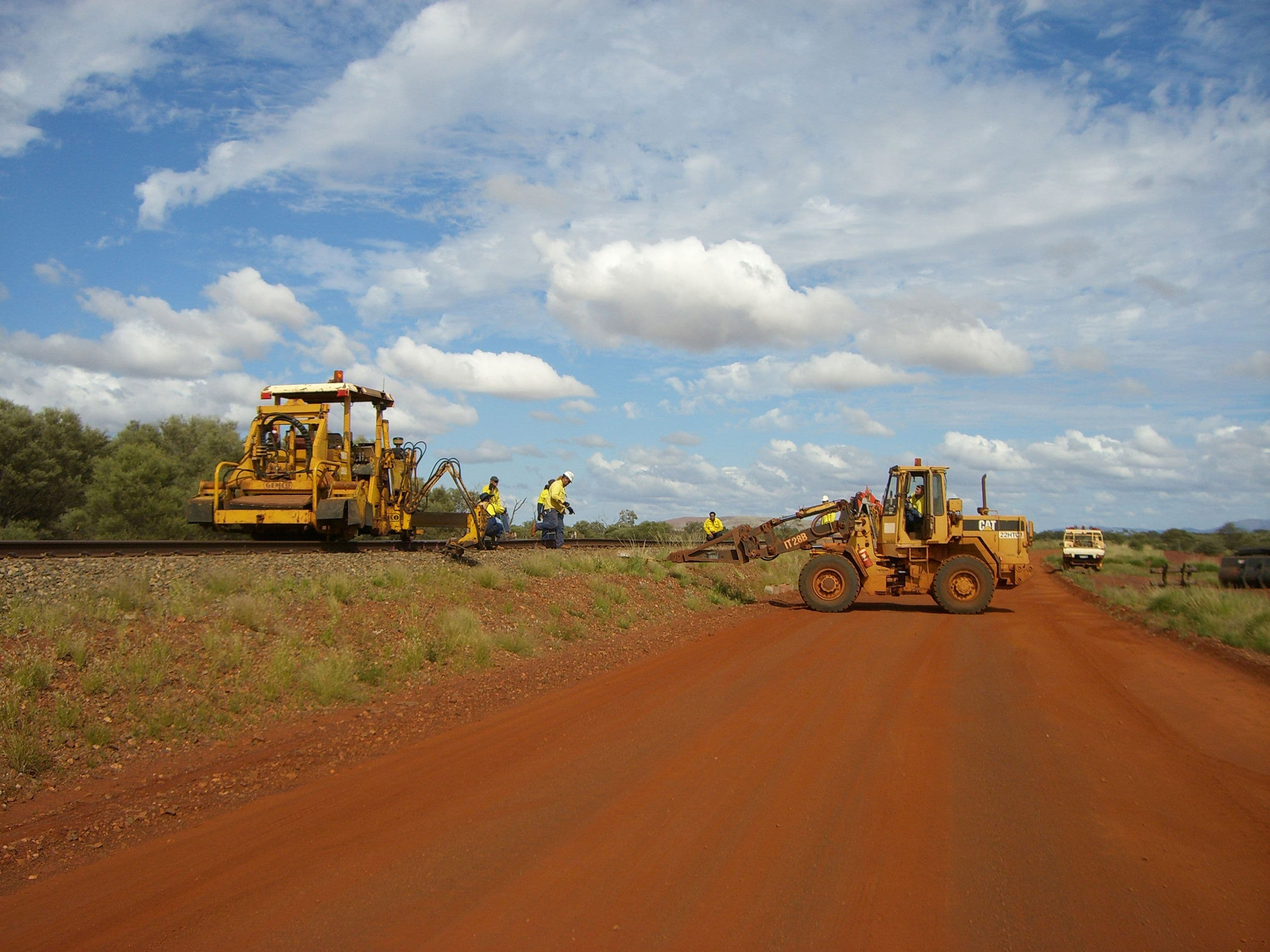
Fluor's Solution
Fluor's contract with Rio Tinto is among the longest running in the company's 100-plus year history. With employees and contracted workers, we have converted the railway from wood to concrete sleepers (or ties) to improve durability and have designed and built approximately 400 kilometers of new track. Since increased traffic was making passing of trains inefficient, parallel tracks for two-way travel were also added.
Other upgrades have improved safety and efficiencies at crossings, turnouts and bridges. In the process, we have developed state-of-the-art expertise in railway services, earned a reputation for excellent safety and quality, and increased the number of workers to meet client needs.
Over the course of the years, we began identifying ways to improve service and add more value to Rio Tinto. We responded by establishing a dedicated re-rail team of people with a broad range of skills and a distinctive depth of experience and knowledge in improving network reliability.
A training program for new workers enabled them to progress from basic to high levels of skills in track work. With a combination of staff and craft and a number of subcontractors, we executed a five-year initiative to repair and upgrade the most worn sections of the railway.
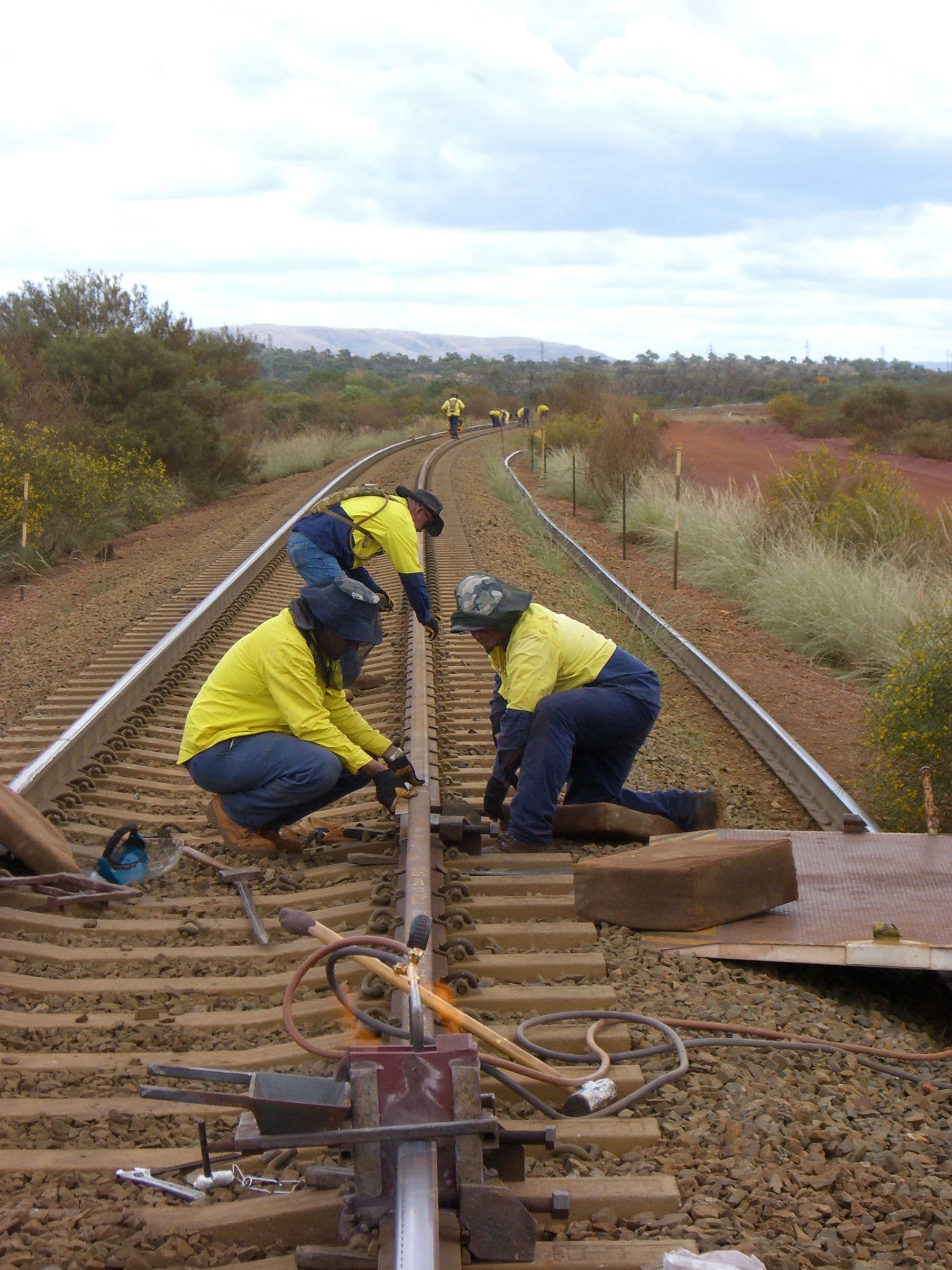
Conclusion
Enhanced maintenance was only part of the overall plan for this railway system, which sprawls over an almost 10,000-square-kilometer area. A Fluor construction contingent continued to address the client's needs for additional track, and an equipment maintenance crew had oversight of the array of machinery used to build and maintain the railway.
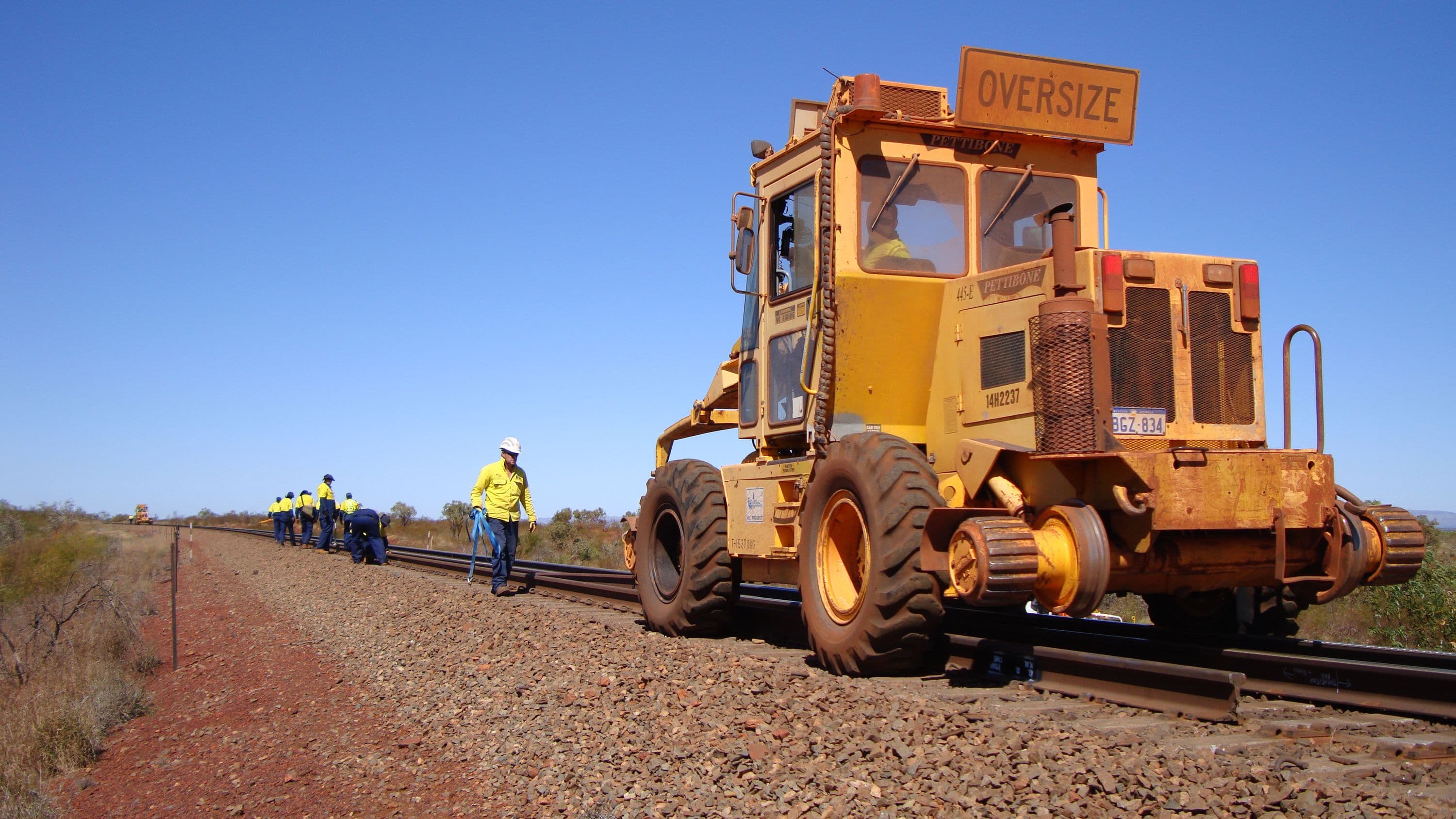