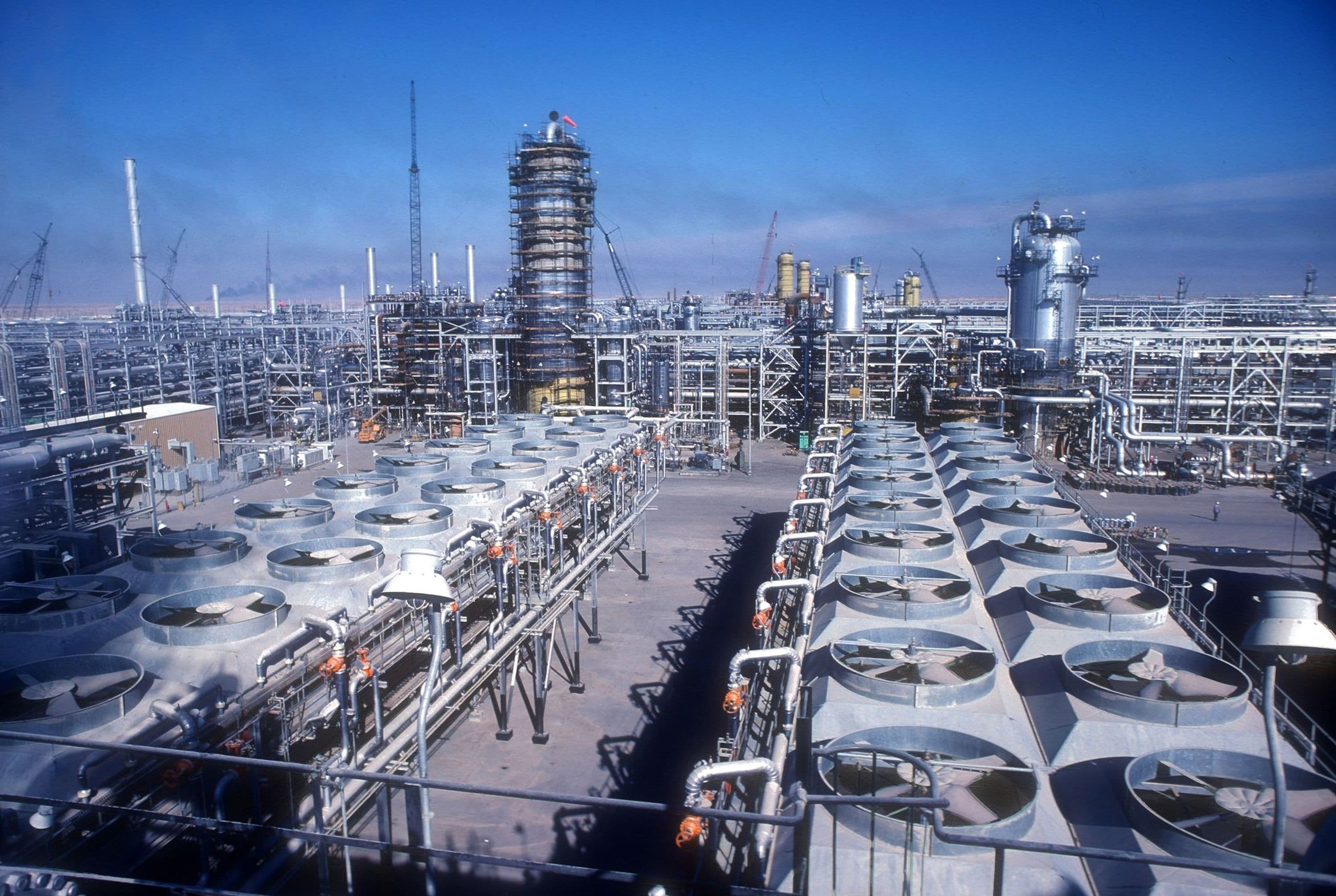
Saudi Aramco Shedgum Gas Plant - EPC
Client: Saudi Aramco
Location: Saudi Arabia
Business Segment: Energy Solutions
Industries: FuelsEnergy Transition

Executive Summary
Fluor provided engineering, procurement and construction management for the Shedgum Gas Plant, which was part of an overall Saudi Arabian gas program undertaken by Saudi Aramco (then ARAMCO) to utilize natural gases previously considered waste product.
In 1977, it was the largest gas-treating program ever undertaken. The Shedgum Gas Plant used the proprietary Fluor EconamineSM technology to remove carbon dioxide, hydrogen sulfide and carbonyl sulfide from the gas.
Client's Challenge
The Saudi Arabian Gas Program was concerned with the oil and gas found in wells in the eastern region of the country, which produced 170 million cubic meters of gas per day associated with 12 million barrels per day of crude oil. The Shedgum Gas Plant was part of a government program to build gas gathering facilities, processing facilities for natural gas liquids (NGLs) and storage and loading facilities to process the gas.
Five billion cubic feet of gas a day from 25 gas oil separator plants were to be processed into sweet fuel gas, ethane and NGL, which was then fractionated to produce ethane for petrochemical feedstock and other gases and gasoline for export.
The main function of the plant was to remove sulfur from the natural gas and to partially fractionate the gas, splitting it into dry and liquid streams for shipment via pipeline to Ju'aymah. The dry gas, mostly methane, was used for fuel and feedstock, while the liquid stream of C2 and heavier hydrocarbons were further fractionated.
The complex fulfilled part of the Saudi Arabian government's huge plan for industrialization of that Middle Eastern nation.
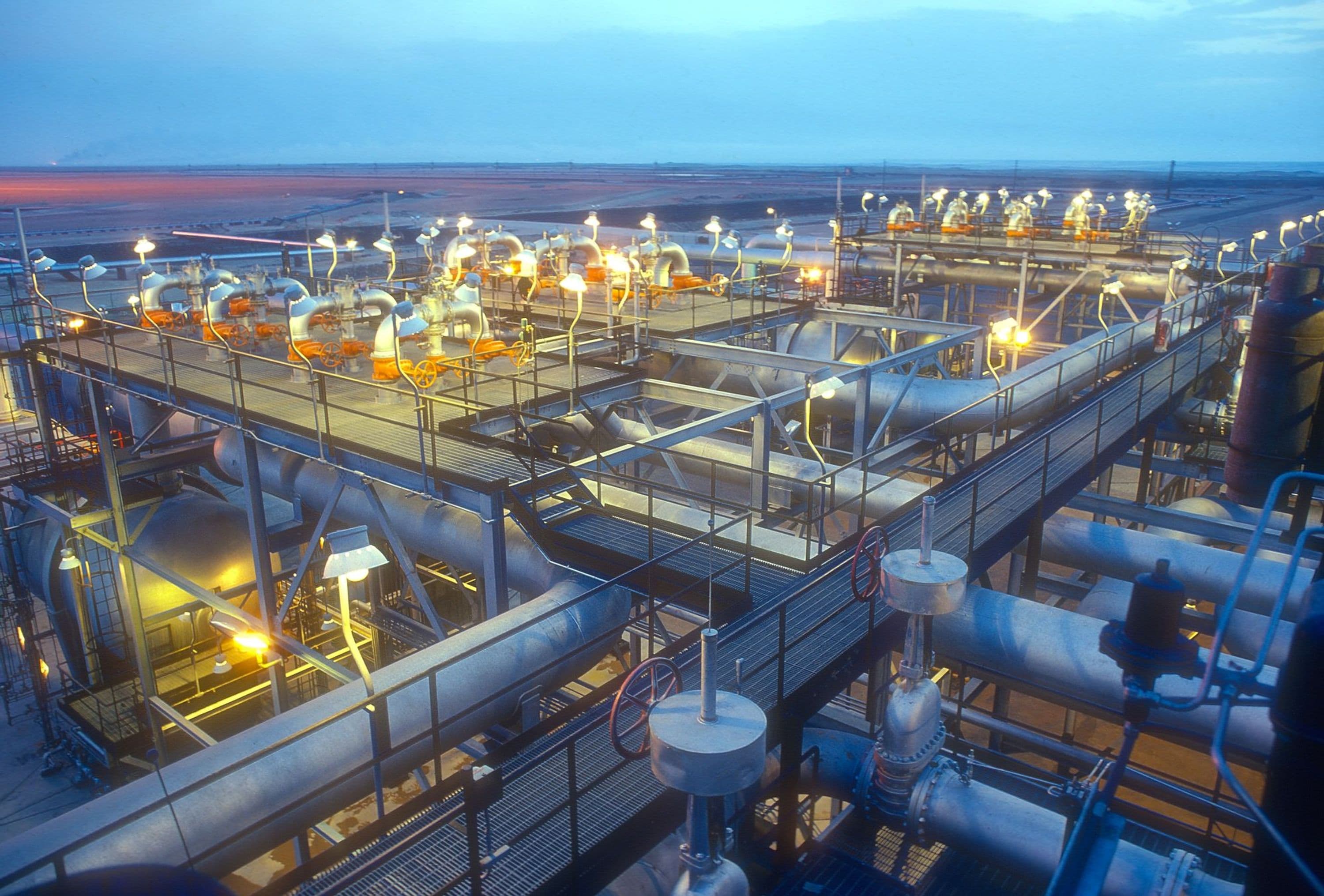
Fluor's Solution
Under Aramco's direction, Fluor engineered the Shedgum plant and procured 800 major pieces of equipment, including vessels up to 357 long tons and pipe racks up to a mile long. Then, we managed the construction work that stretched from the completed Berri plant on the Arabian Gulf, 97 km down the coastline to the marine terminal fractionation center at Ju'aymah, and 193 km (120 miles) inland to another gas plant at Uthmaniyah.
Only two years into construction, there were 29 jobsites with 1,300 Fluor employees supervising Fluor labor and contract workers expected to peak at 25,000.
Four identical modules enabled the plant to process 1.4 billion cubic feet per day of gas. The craft workers and laborers who put these mammoth projects on the ground faced temperatures up to 54° C in the summer and shamals (storms of blowing sand) that could be as blinding as a blizzard.
Aramco chose to utilize the Fluor Econamine chemical absorption process to remove carbon dioxide, hydrogen sulfide, and carbonyl sulfide from the gas. This process, employing diglycolamine (DGA), was superior because it was efficient at higher concentration without causing serious corrosion. It also operated efficiently at temperatures attainable at the site with only air-cooling.
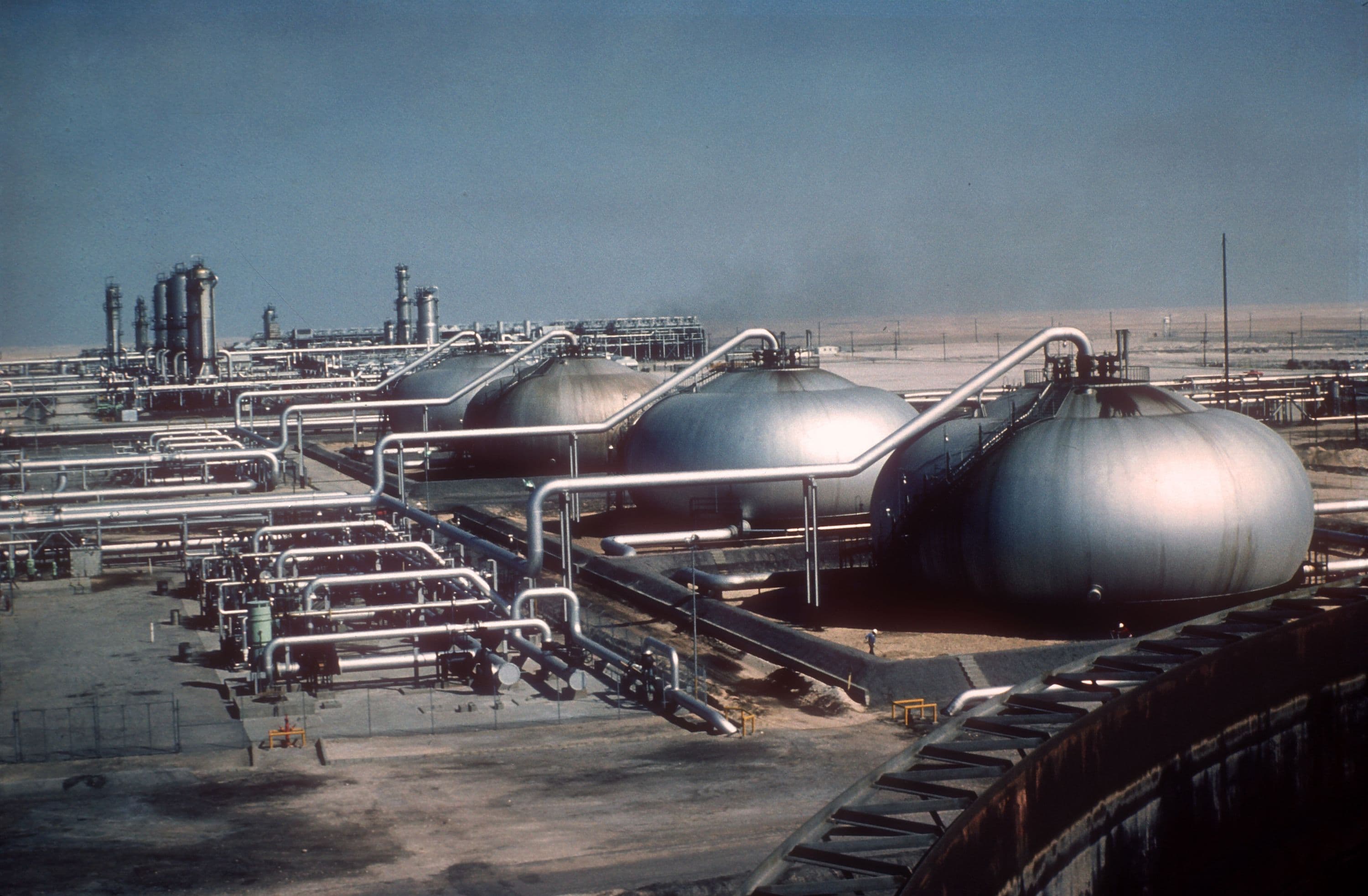
Conclusion
Conserving and utilizing natural gases that previously were flared was basic to the industrialization of the Kingdom of Saudi Arabia.
When it was constructed, the gas plant facility at Shedgum, covering 1 million square feet of desert soil, was one of the largest NGL fractionation plants in the world. Today, it is the largest.
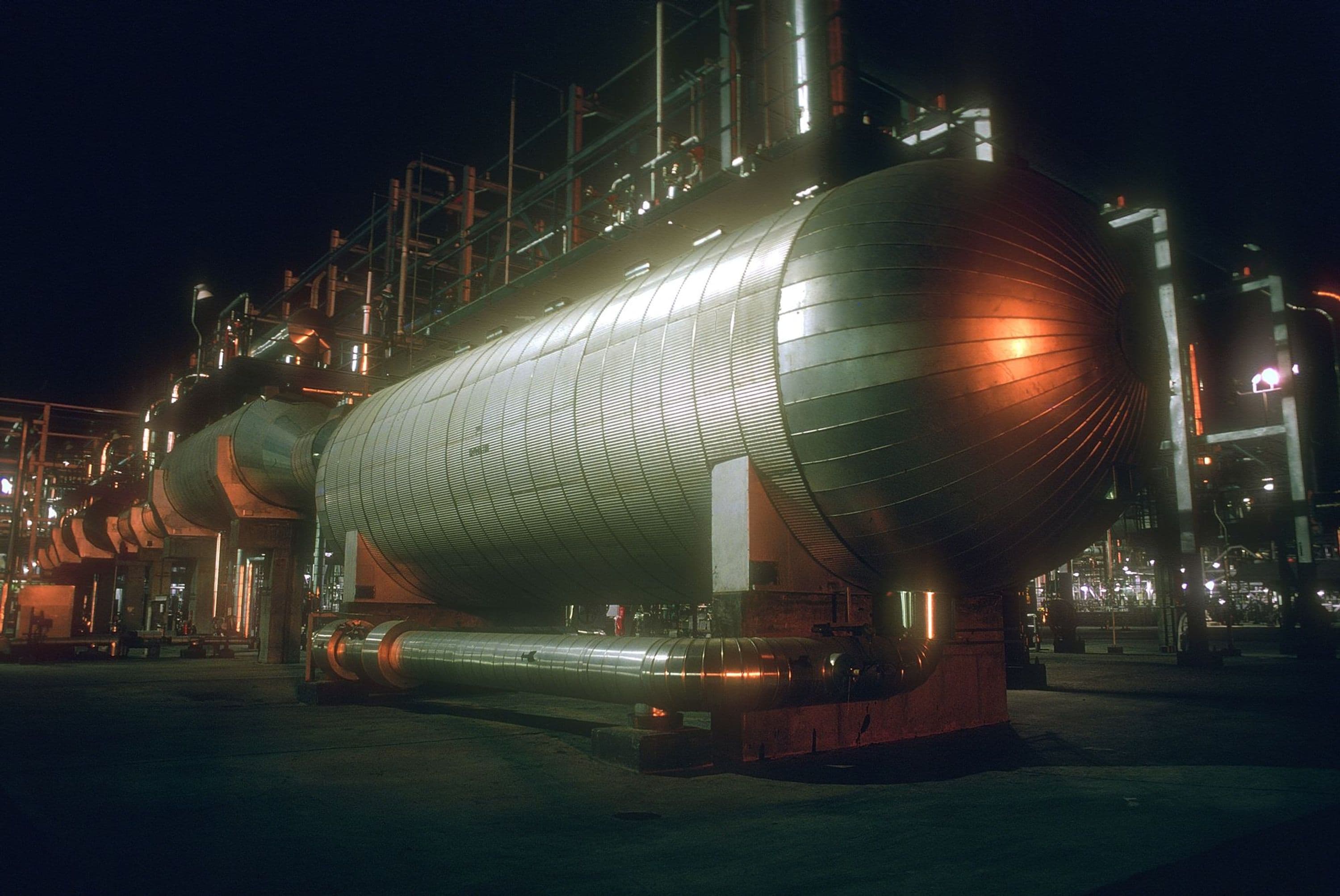
Project Gallery
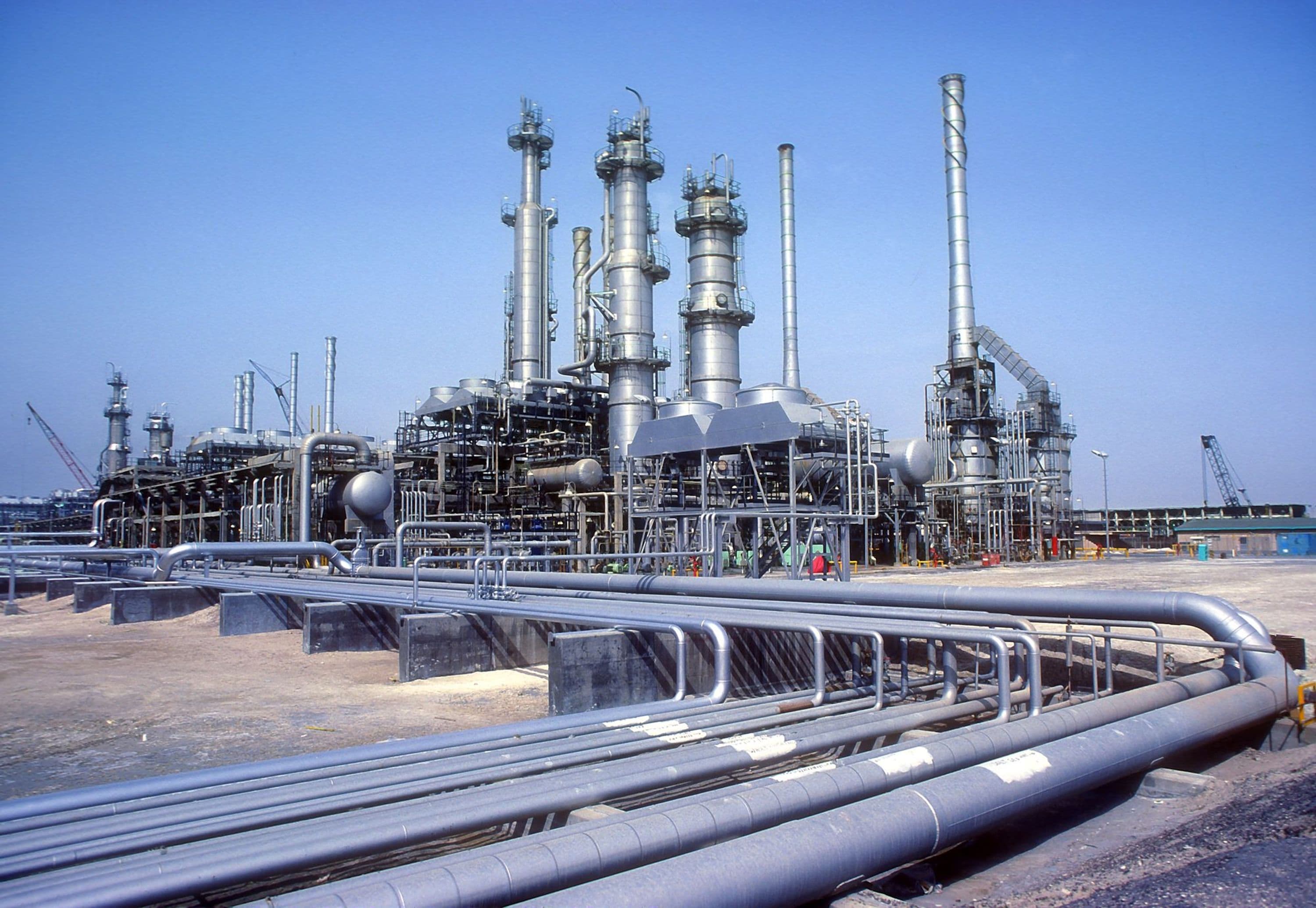
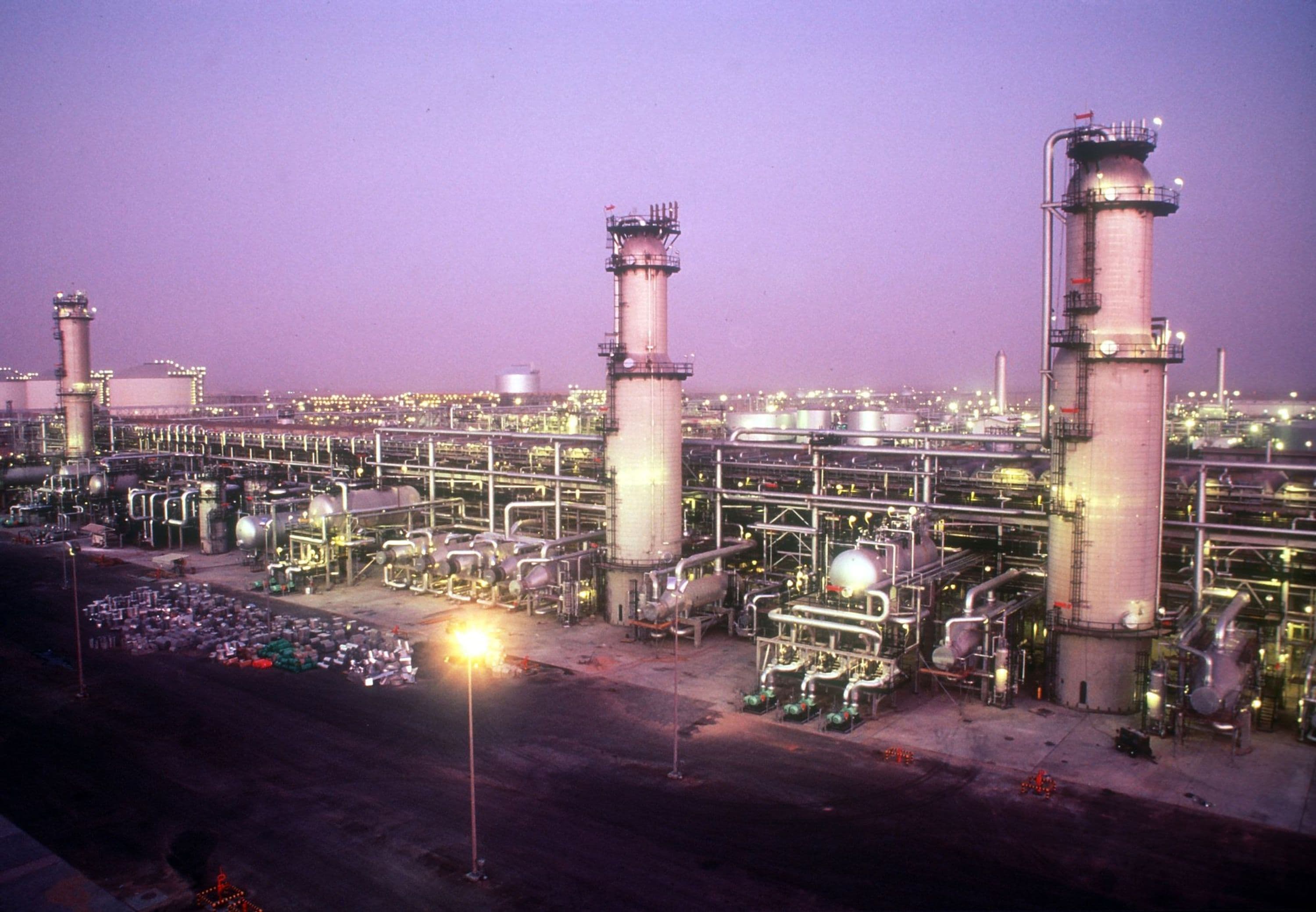
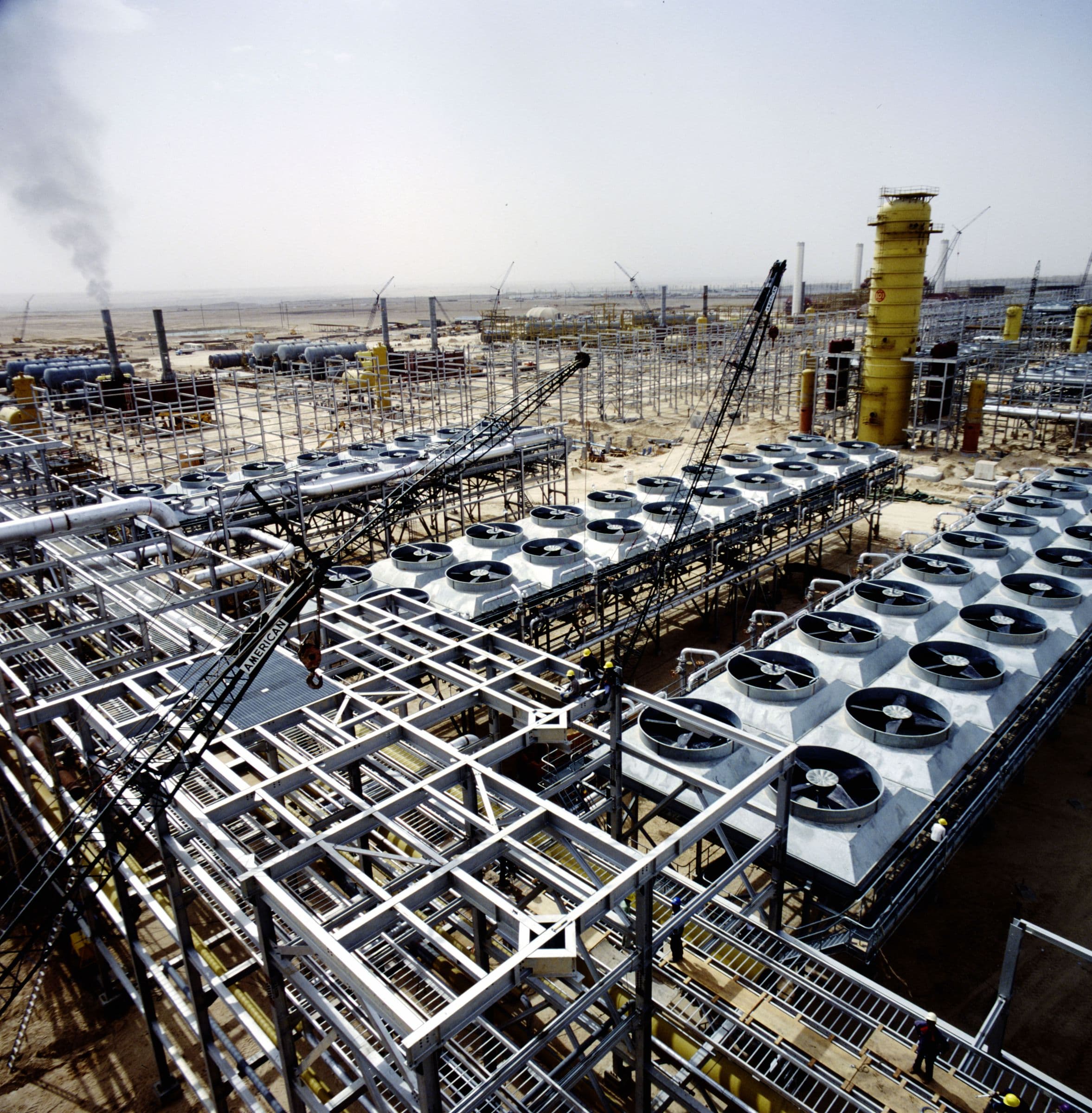
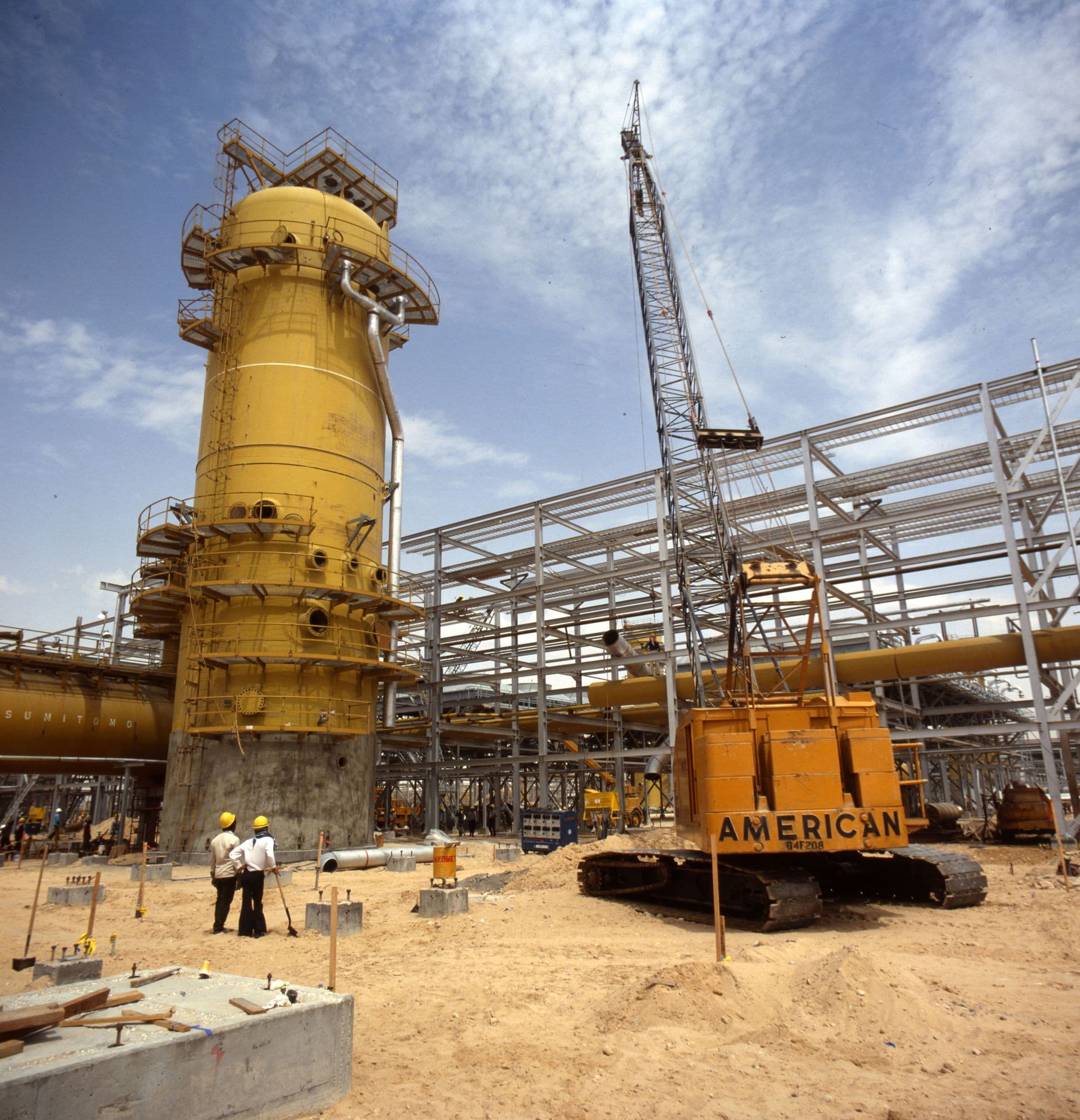