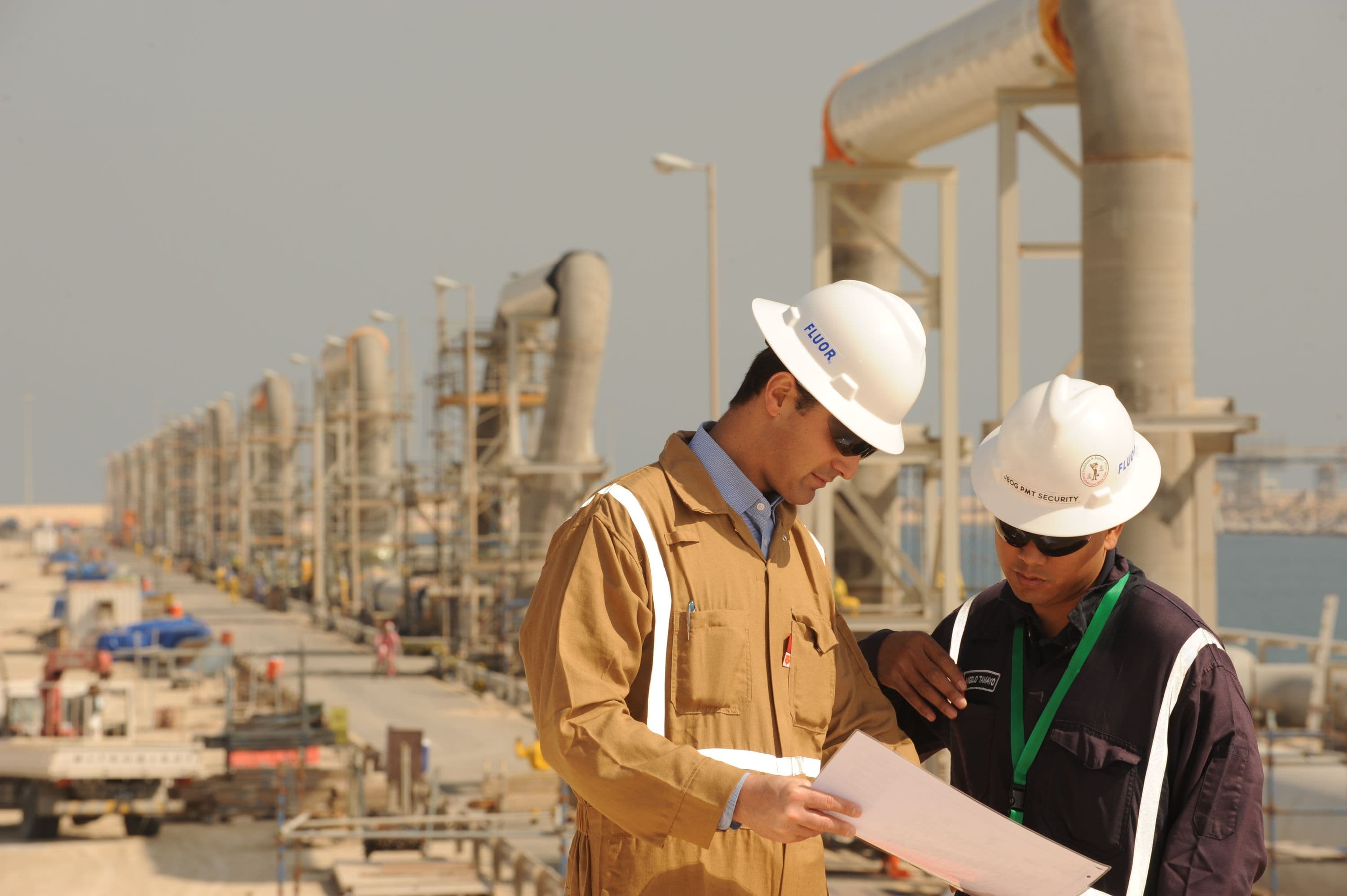
Qatargas Jetty Boil-Off Gas Recovery
Client: Qatargas Operating Company Ltd.
Location: Ras Laffan, Qatar
Business Segments: Energy SolutionsUrban Solutions
Industries: InfrastructureEnergy TransitionFuels

Executive Summary
Fluor performed front-end-engineering and design (FEED) and developed a capital cost estimate for the gas loading and boil-off facilities at Ras Laffan. We were later awarded the engineering, procurement and construction management (EPCm) contract for the project.
The Jetty Boil-Off Gas Recovery is a world-scale environmental project to minimize the amount of gas flared at Ras Laffan to the fullest extent practical. This is done by recovering and collecting the boil-off gas at each berth and using it elsewhere as fuel gas. The development was completed in 2014, with the first cargo of boil-off gas recovered in October.
With the successful start-up, Fluor entered into a two-year warranty period to ensure the facilities operated as intended. The project has recovered more than 1.12 million metric tons of boil-off gas from 1,200 different ships, a recovery rate of more than 93%.
Client's Challenge
Qatargas Operating Company, Ltd. is an agent for seven Qatar liquefied gas companies and Ras Laffan liquefied natural gas (LNG) companies.
Recovery systems eliminate pollution and supply fuel gas to LNG companies at the Qatargas terminal. Natural gas is cooled to approximately -250° Fahrenheit for shipping, which also condenses it. Jetty boil-off gas is generated through vapor displacement from ship loading and vaporization. It had been flared at LNG loading berths.
Approximately 168 tons per hour of boil-off gas, the volume produced from three berths loading simultaneously, was recovered at one of the first systems. Roughly 78.3 million metric tonnes per annum of Qatar LNG will be exported from the Ras Laffan port when all the Qatargas and RasGas expansion projects are completed.
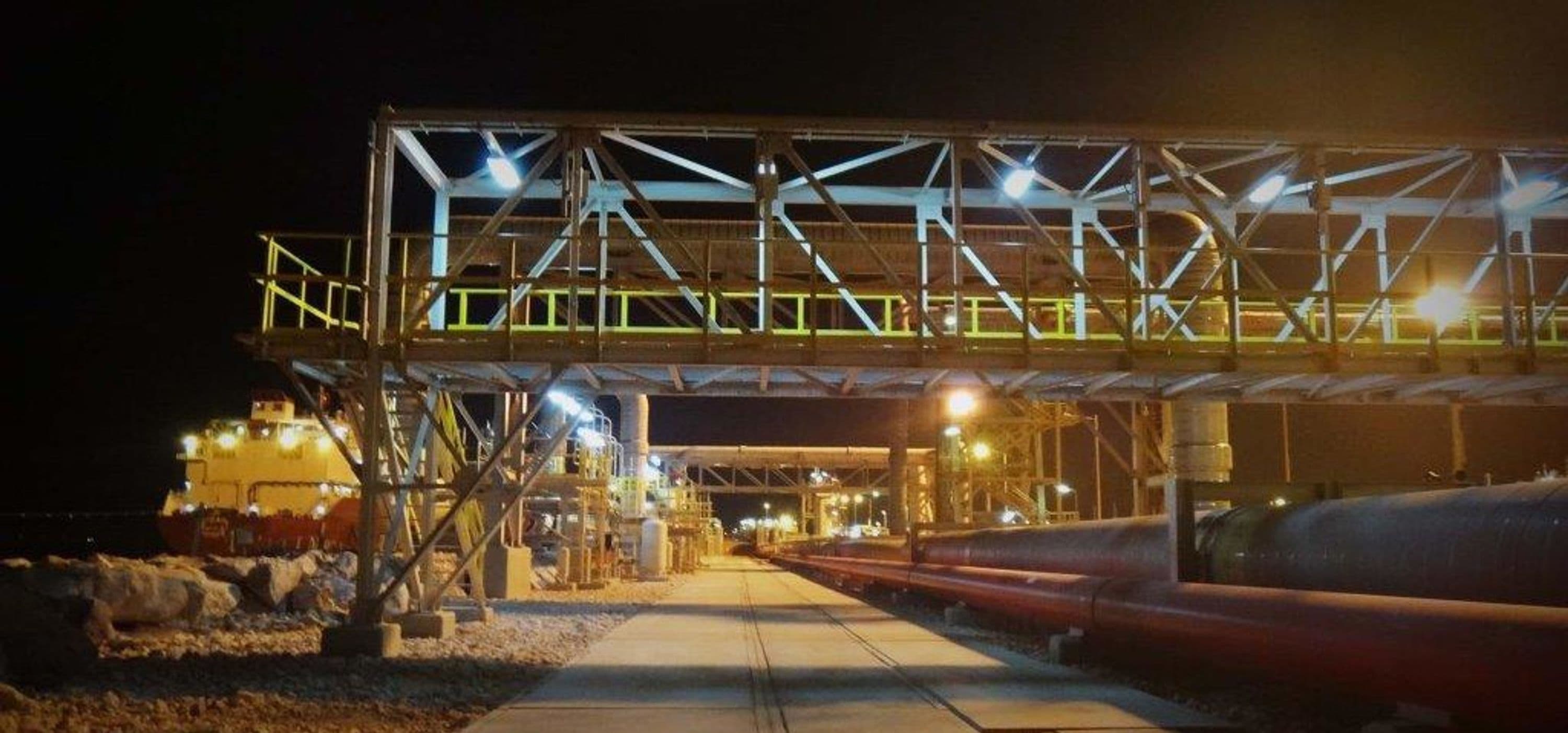
Fluor's Solution
The objective of Qatargas at Ras Laffan was to eliminate to the extent practicable flaring of boil-off gas. We performed FEED, enabling gas to be piped via a large-diameter header to a central compressor and delivered as fuel gas. Gas not consumed as fuel gas was to be further compressed through a sales gas pipeline compressor, to supply the Mesaieed pipeline. Later, we performed EPCm on this project. Our scope also included a two-year warranty period, continuing our focus on client excellence and supporting project operations.
The JBOG system consists of a gas gathering piping network at the berths, a 60-inch header, two compressor trains and a gas distribution piping network to the end users. Each train of compressors consists of a low-pressure (LP A & B), medium-pressure (MP A & B) and high-pressure (HP A & B) compressor. Each train has been designed to compress 81.5 tonnes/hour of gas from 0.03 barg to 47.6 barg. When both compressor trains operate at full design capacity, 163 tonnes/hour of BOG will be delivered to the end users.
&w=3840&q=75)
Conclusion
The Jetty Boil-Off Gas project would minimize the amount of gas flared at Ras Laffan to the fullest extent practical by recovering and collecting the boil-off gas at each berth and using elsewhere as fuel gas. We performed FEED and a capital cost estimate prior to being awarded EPCm for the project. Engineering was performed by our Houston and New Delhi offices.
Qatargas Operating Company awarded the project its 2013 HSE Excellence Award. Upon completion of the development, Fluor continued project support during a two-year warranty period, which concluded in 2016.
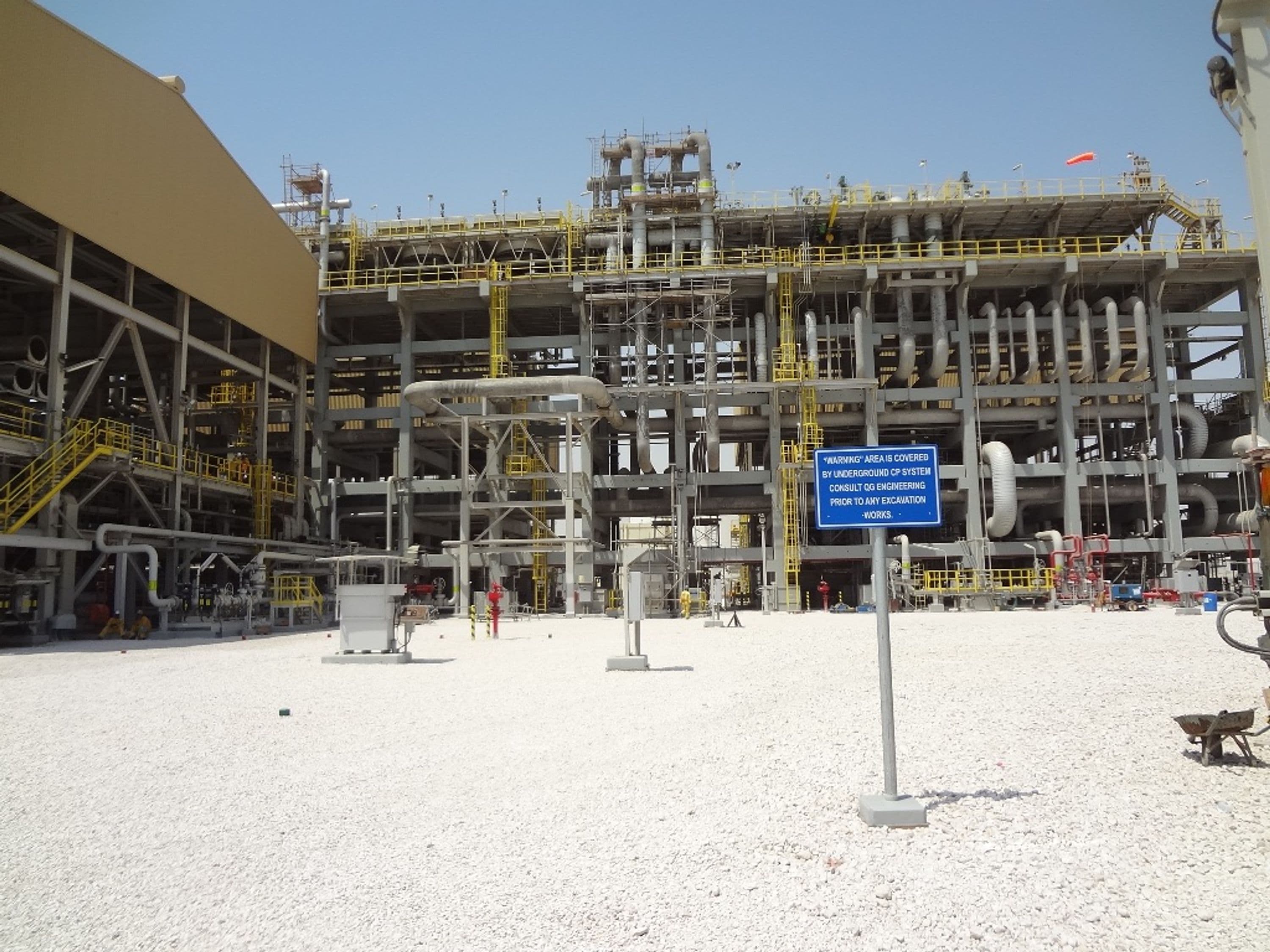