&w=3840&q=75)
Logan Aluminum Rolling Mill
Client: Logan Aluminum
Location: Kentucky, U.S.
Business Segment: Urban Solutions
Industry: Mining & Metals

Executive Summary
To meet the beverage industry's growing demand for light gauge, tight-tolerance aluminum sheet stock, Logan Aluminum committed to a major capital expansion project. A critical requirement during the project execution was the continual operation of the existing mill without production disruption.
Fluor was selected to provide engineering, design, procurement, construction, start-up and maintenance. Built at a cost of over $400 million, the plant was designed for an initial output of 400 million pounds of aluminum coil stock annually with provisions for expansion to one billion pounds. The new facility included a 300,000-square-foot building with state-of-the-art high-speed production and material handling equipment. The Logan Expansion project was completed on schedule and under budget.
Client's Challenge
The goal of the large-scale expansion project was to build a state-of-the-art mill to supply the light gauge, tight tolerance sheet metal for the beverage market. A critical requirement during the project execution was the continual operation of the existing mill without production disruption. The client's stringent product requirements were sheet quality, gauge uniformity, flatness and cleanliness of the thin aluminum sheet stock.
The new facility included a 300,000 square foot building with state-of-the-art high-speed production and material handling equipment. The plant was designed to handle ingots weighing 60,000 pounds each.
Highly automated, the plant required extensive software and hardware design provided by both systems vendors and our automation services team. The newly installed cold mill ran 6,000 feet per minute. It included coolant and environmental controls. The slitter ran 4,000 feet per minute. The packaging unit handled 9-foot diameter rolls at 7 feet wide with capability to wrap both horizontal and vertically.
We installed and operated our proprietary Computerized Maintenance Management System at the plant. It provided a planned approach to maintenance and stored information on over 21,000 equipment items and 15,000 stores inventory items.
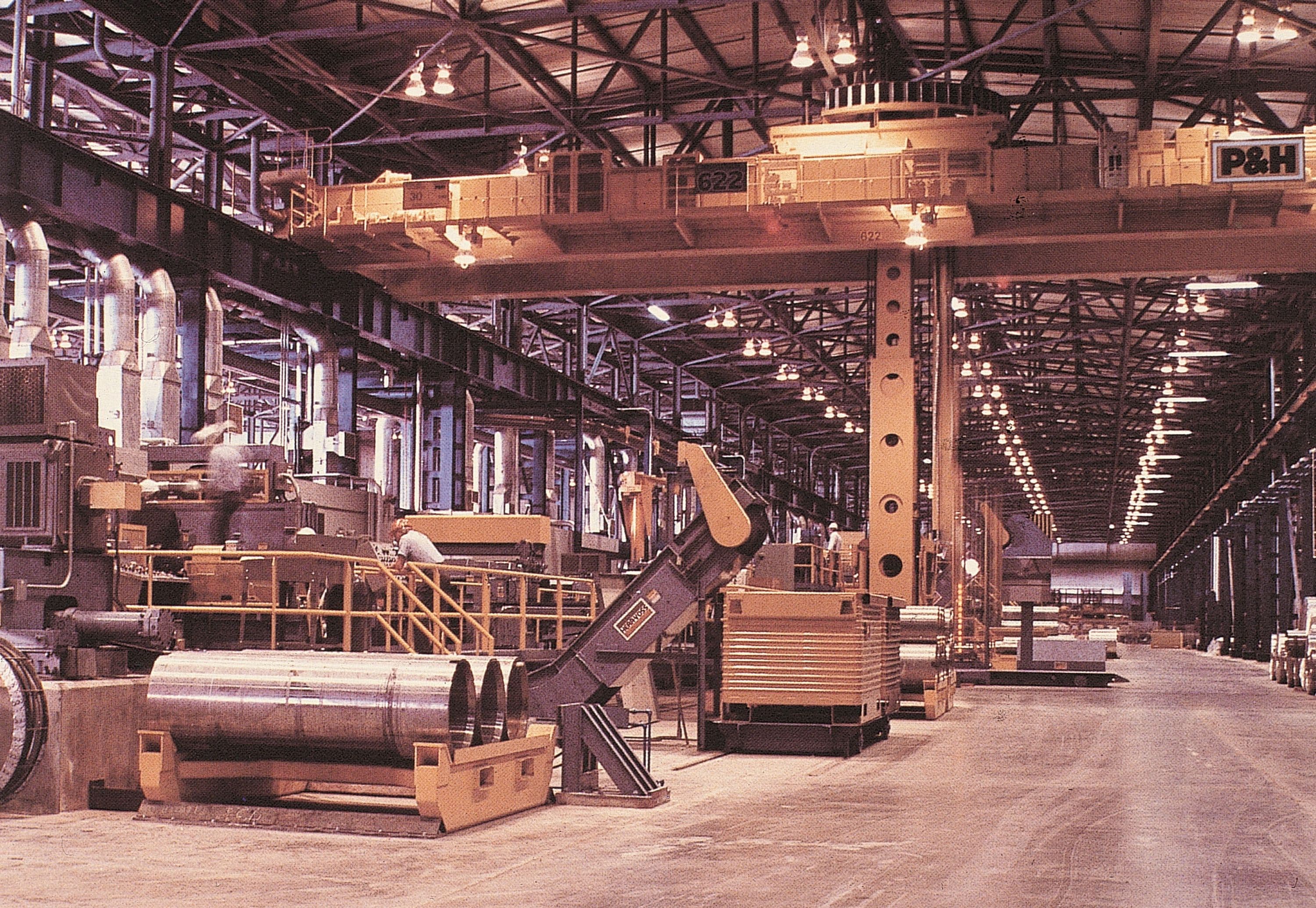
Fluor's Solution
The design and construction of this world-class aluminum casting and rolling mill presented our design-build team with one of the most challenging assignments undertaken in the history of the metals industry. Built at a cost of over $400 million, the plant was designed for an initial output of 400 million pounds of aluminum coil stock annually with provisions for expansion to one billion pounds. Management and execution of a total services program of this magnitude established both Fluor and industry records.
Over 750,000 work hours of engineering and 3,000 drawings were required. The plant was designed to handle ingots weighing 60,000 pounds each. The hot mill alone, manufactured by Blaw Knox, cost over $35 million. Electrical equipment purchased from GE cost over $33 million. More than 4.3 million work hours of craft labor were expended.
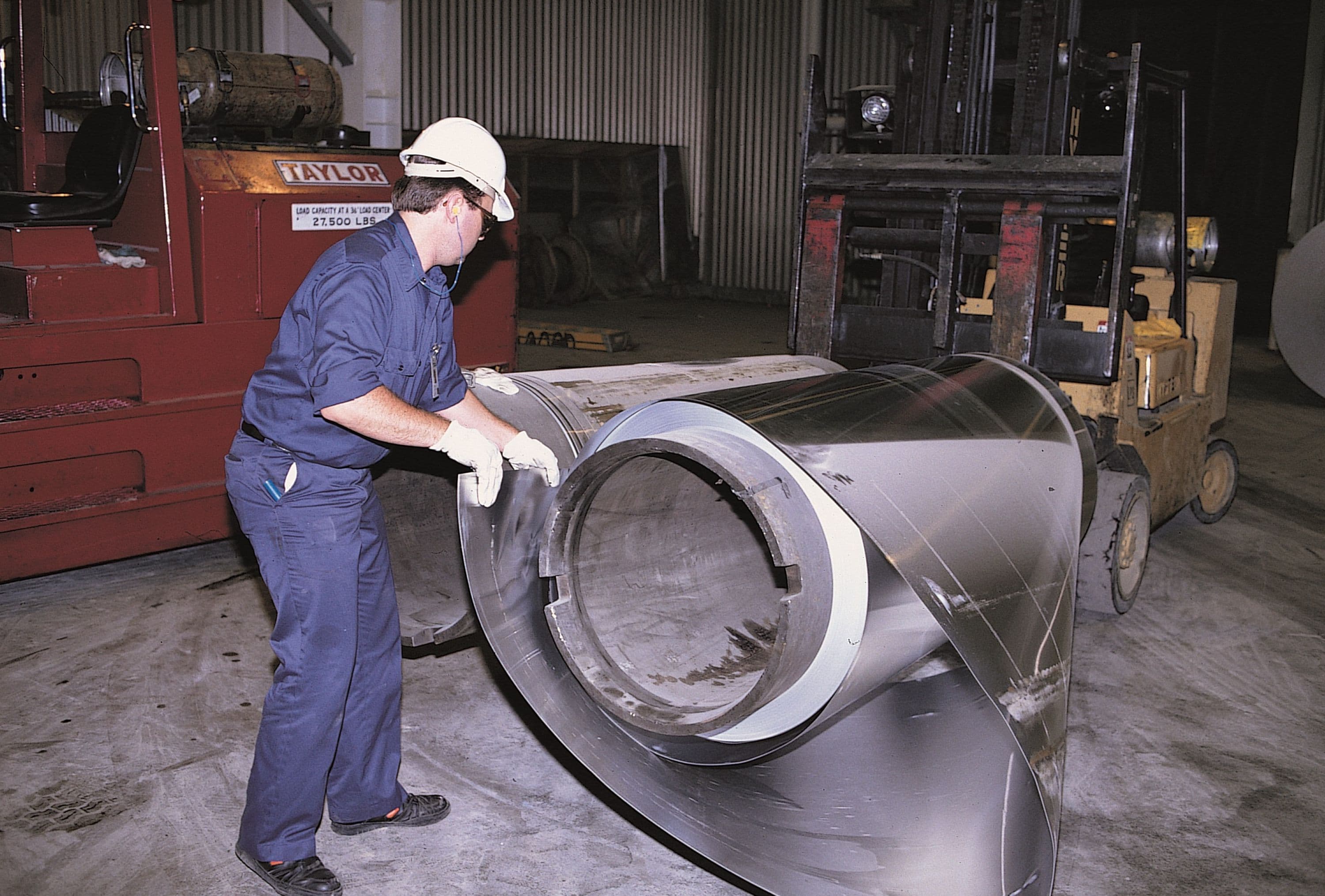
Conclusion
The Logan Expansion project was completed on schedule and under budget.
Both Logan Aluminum and Fluor were honored by the Project Management Institute with recognition of the 1994 International Project of the Year Award.
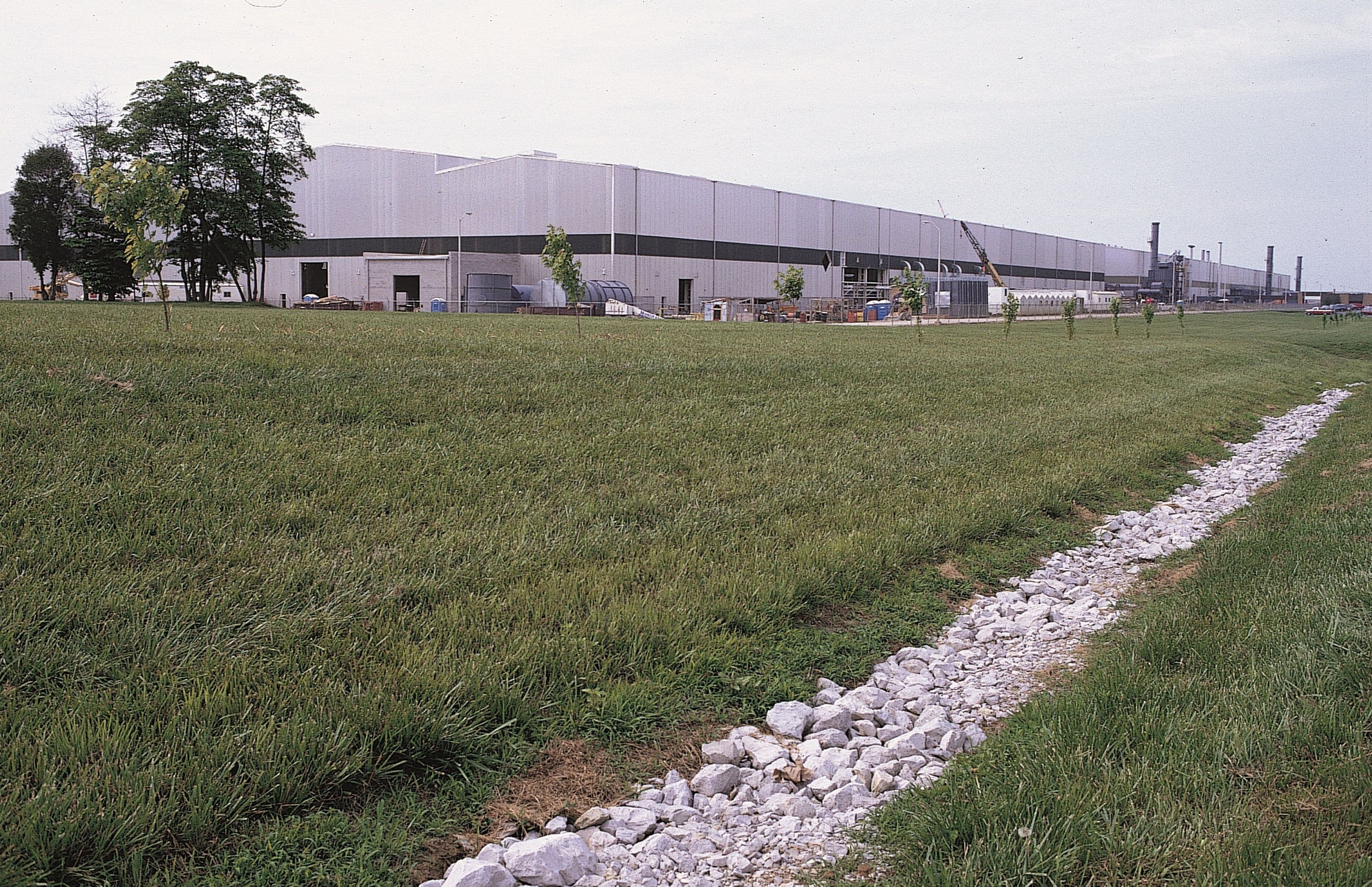