&w=3840&q=75)
Constellium Project Quiver
Client: Constellium-UACJ
Location: Bowling Green, KY, U.S.
Business Segment: Urban Solutions
Industry: Mining & Metals

Executive Summary
Constellium-UACJ contracted with Fluor for engineering, procurement and construction (EPC) of a new 100,000 metric tons per annum aluminum automotive sheet facility in southwestern Kentucky. The green field manufacturing facility, located in a Bowling Green industrial park, would be supplied by cold rolled coils from both partners' rolling mills. This capital investment would be one of the largest in the region in more than a decade, according to local officials.
Client's Challenge
After U.S. government agencies had issued joint rules to establish Corporate Average Fuel Economy (CAFE) and Greenhouse Gas emission standards for automotive vehicle model years 2017 and beyond, original equipment manufacturers (OEMs) sought ways to reduce the weight of vehicles. As a result, industry demands for automotive aluminum sharply rose to meet this new market condition.
Constellium and UACJ, global producers of aluminum products, signed a joint venture agreement in May 2014 to supply body-in-white aluminum sheets to the North American automotive market. The manufacturing facility would provide products from technologies developed from each European and Japanese partner. The Bowling Green site was selected for its central location to supply automotive OEMs across the U.S., skilled local labor force and the entrepreneurial spirit of the area. The site accommodated the initial target capacity plus future expansion considerations.
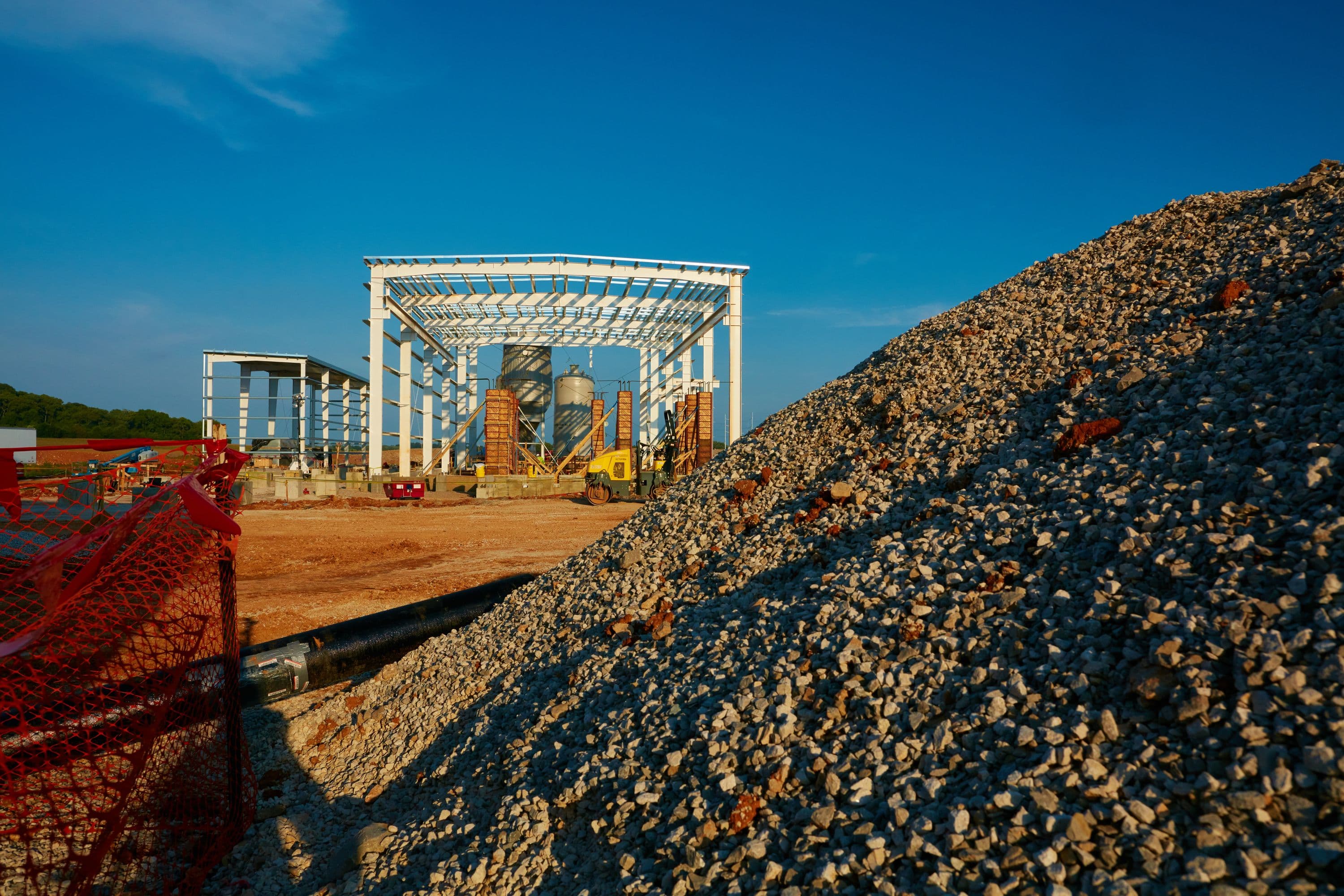
Fluor's Solution
After providing front end loading engineering services, environmental/building permitting assistance and site selection activities, we provided EPC services for the initial 235,000 square foot plant. More than 500 workers were onsite at the peak of construction, and more than 500,000 work hours were safely completed. We participated in the KY OSHA Construction Partnership Program (CPP), which helps maintain safe worksites and promote health and safety in the construction industry.
We used our global dispersed execution approach for home office services and relied on a Fluor subsidiary to provide construction equipment and consumables to meet the extremely aggressive schedule. We provided self-perform construction services for the mechanical equipment setting, piping, electrical, instrumentation/control systems and selected concrete foundations works.
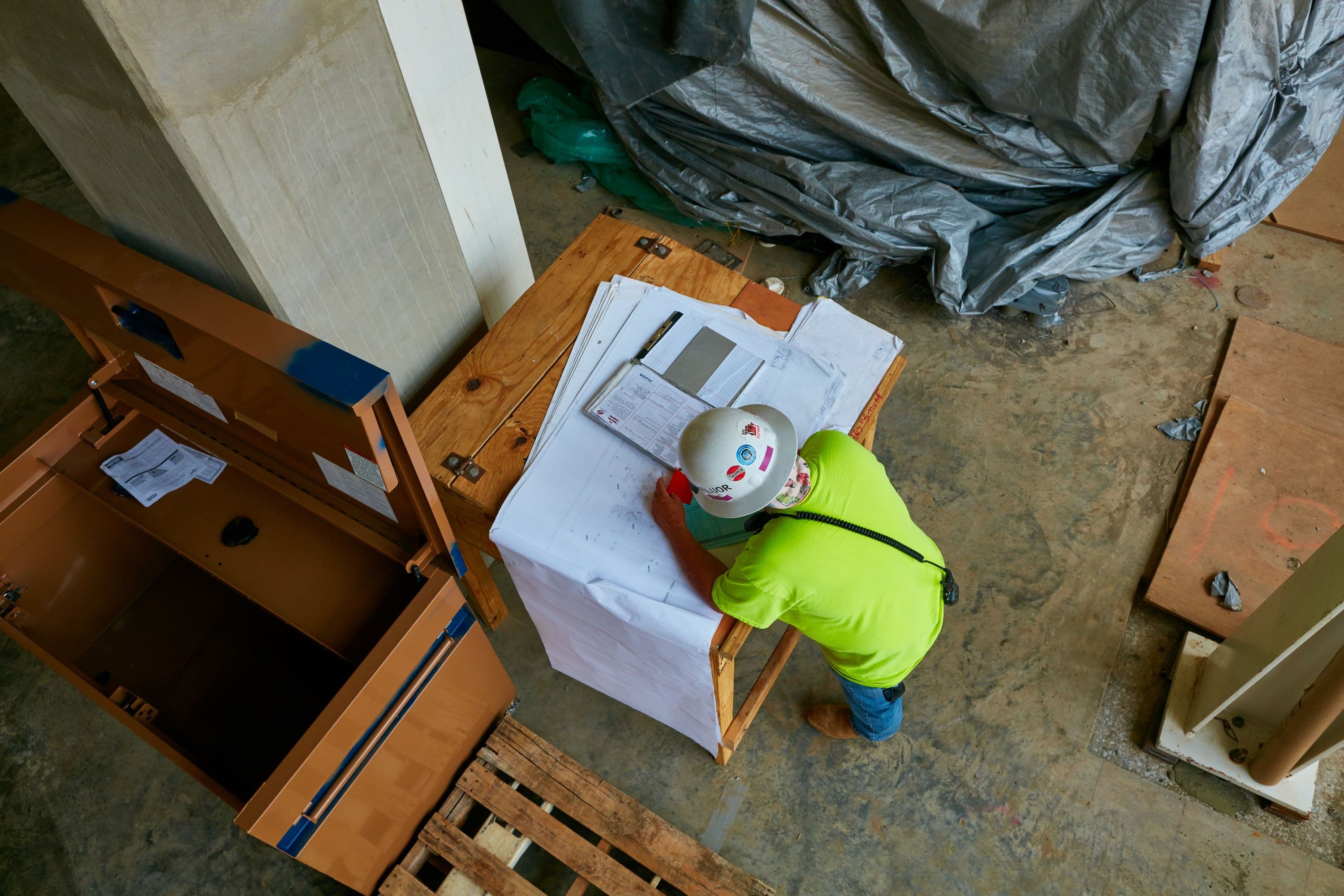
Conclusion
Fluor worked closely with the owner, local and state agencies, consultants, equipment suppliers, local utilities and area contractors to transform the former wheat field into a quality automotive aluminum manufacturing facility in less than 18 months from breaking ground.
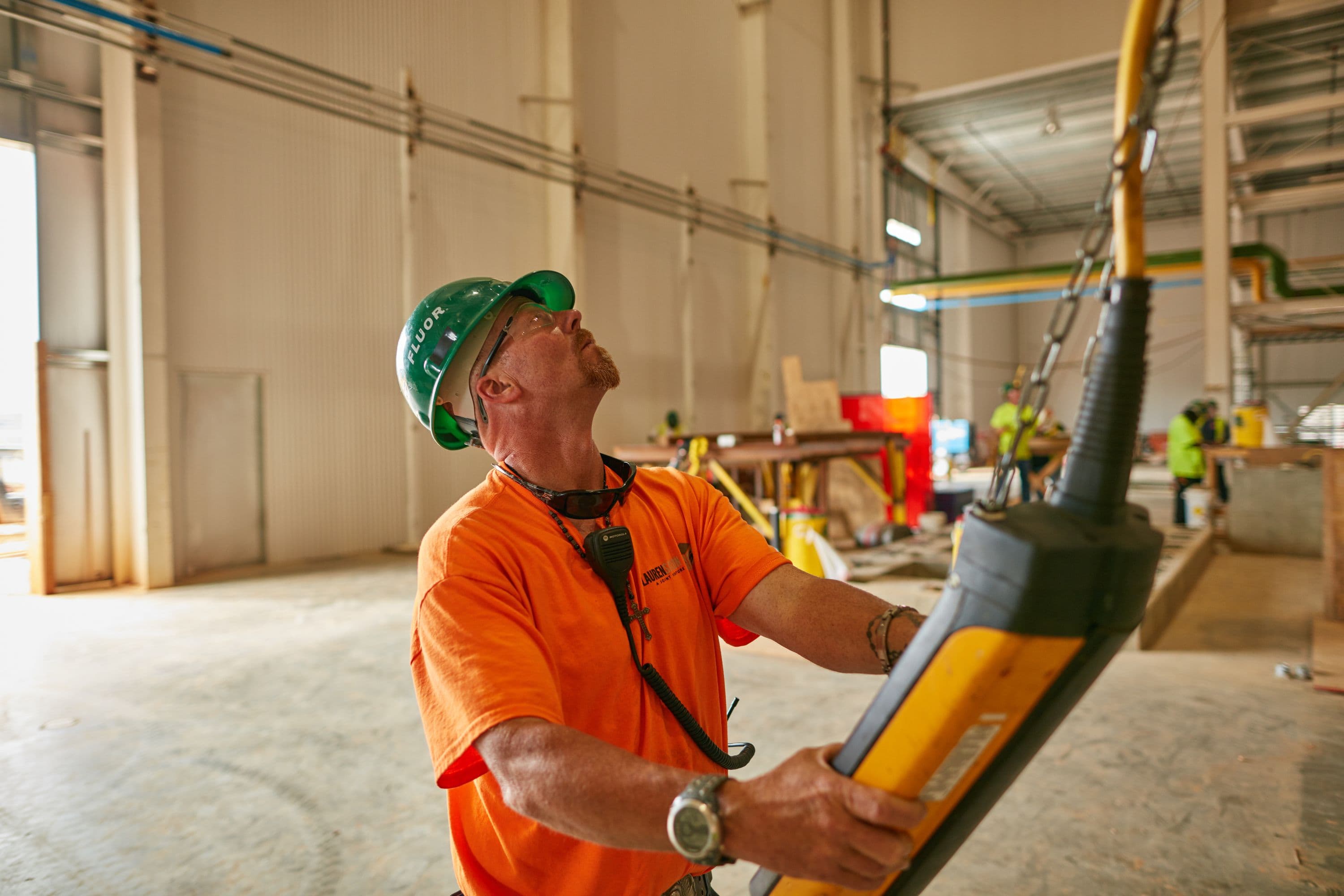