Abstract
Fluor's experience with ultra-low sulfur diesel applications has continually emphasized the importance of reactor internals in evenly distributing the liquid phase of the reactor over the entire catalyst surface. Uneven liquid distribution at the top of the bed reduces catalyst utilization, necessitating a high overall reactor temperature to meet product specifications. Such adverse conditions can negatively affect performance and Fluor technology provides the uniform liquid distribution through Reactor Internal technology like the swirl cap distribution tray and the swirl zone quench mixing device. The use of each promotes safety for a variety of applications.
Fluor clients are able to get open art technology for their projects without going to a process licensor or contractor. This is better, faster and cheaper.
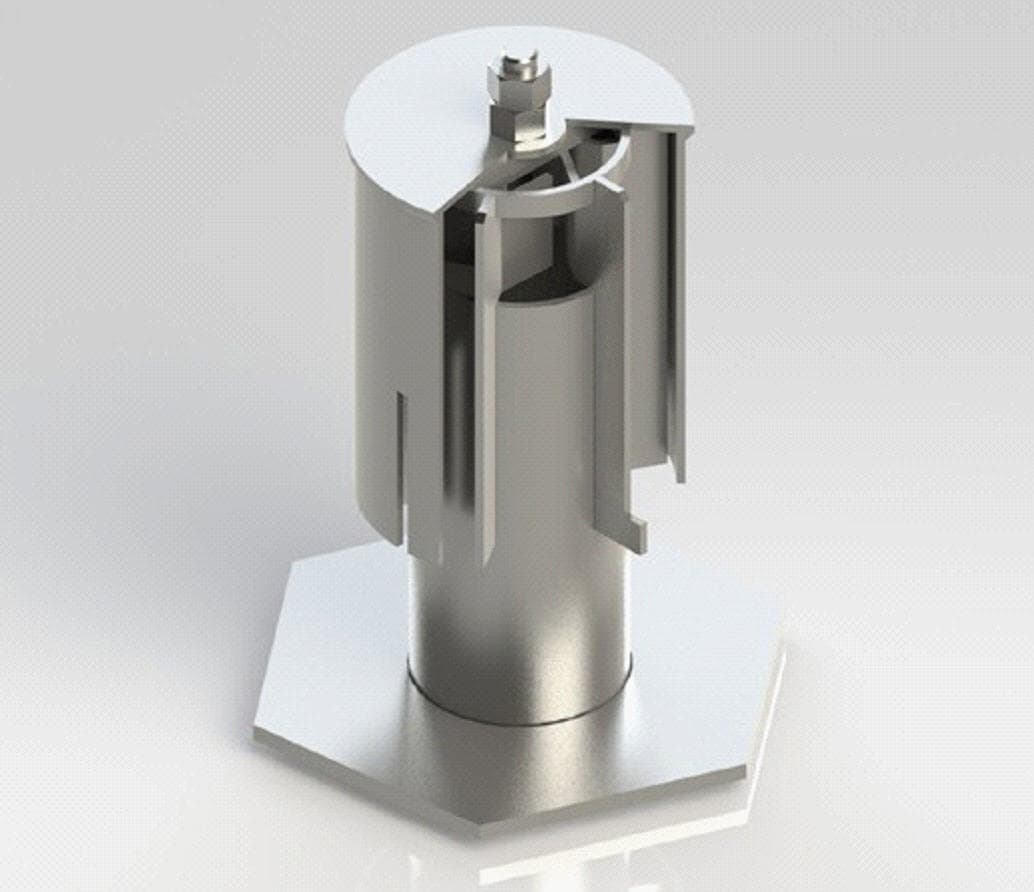
Client Benefits
Fluor's hydroprocessing technologies, like the innovative patented fixed-bed reactor internals, help clients:
Retain more flexibility in selecting catalyst technology providers while Fluor retains complete control in the design of critical path reactors
Maximize the use of catalyst by uniform liquid / vapor distribution
Allow for better catalyst utilization and longer life
Provide opportunities for capitalizing on cost and schedule efficiency