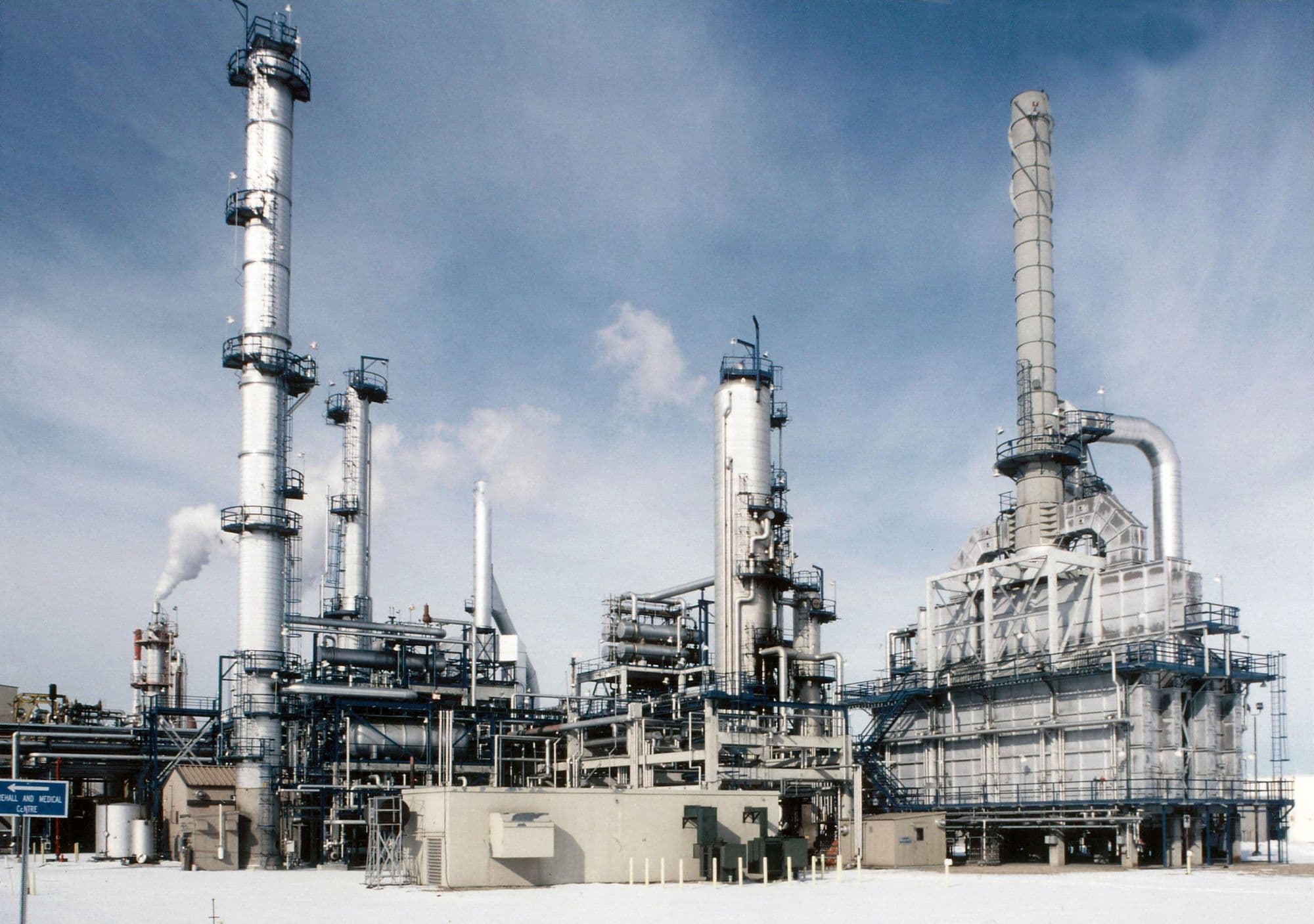
Propane and Ethane Recovery Processes
- Home/
- Services and Expertise/
- Innovation and Expertise/
- Technologies & Processes/
- Propane and Ethane Recovery Processes
Propane and Ethane Recovery Processes
Abstract
Fluor's patented propane and ethane recovery technologies are turbo-expander-based processes configured to recover propane and ethane contents from a variety of feed gases. Our propane recovery process can economically recover 99.9% propane in the feed gas, providing a lean gas that can be used for sales or for liquefied natural gas (LNG) production, while our ethane recovery process can recover over 95% of the ethane content and can be switched between ethane and propane recovery mode while maintaining high recoveries and efficiencies. These processes are suitable for grassroot facilities, but can also be used in retrofitting existing plants for higher efficiency. The process can handle feed gases with variable amounts of nitrogen while maintaining the recovery efficiencies. We have designed more than 80 turbo-expander plants since 1990 with single train capacities as high as 1500 MMscfd.
Client Benefits
Clients come to Fluor looking for solutions to optimize propane and ethane recovery. We offer clients:
Various patented configurations for customizing plant feed gases and conditions
Flexible operation and energy efficiency
Innovative designs based on proven plant operations
Patented designs with lower capital and operating costs than competing costs
Modularized equipment, saving in installation costs
Optimized project schedules for plant operations and production
Cryo-GasSM Process:
Fluor's Cryo-Gas Process portfolio of patented propane and ethane recovery technologies is applicable for both conventional gas and unconventional gas.
Deep Dewpointing Process (DDP):
DDP is a standard module designed for shale gas applications, with ethane liquid contents of 6 to 12 GPM and feed pressure ranging from 500 psig to 900 psig. The process can achieve 95% propane recovery in full ethane rejection mode and can recover 60% ethane in ethane recovery mode. The process has a high turndown capability, similar to conventional MRU plants and does not require the use of turbo expander.
In 2019, Fluor's DDP technology won Best Gas Processing/LNG Technology at the Hydrocarbon Processing 2019 Awards gala event.
Vapor Reflux Absorption Process (VRAP):
VRAP has a low capital cost, weight and footprint. It is ideal for offshore applications requiring propane recovery of over 99% without external refrigeration.
Two-column, High-pressure Absorber Process (TCHAP):
TCHAP is a high-pressure absorber operation that avoids CO2 freezing issues and can produce high pressure residue gas suitable for pipeline operation and feed gas to LNG liquefaction plants. It can be designed to fully reject ethane without loss in propane recovery and can achieve less than 500 ppmv CO2 in the ethane product. TCHAP is suitable for high-pressure feed gas over 1,000 psig and ethane recovery of more than 80% with propane recovery of 99%.
Twin-reflux Absorption Process (TRAP):
TRAP is an integrated ethane and propane recovery design utilizing deethanizer overhead for refluxing during propane recovery and ethane reabsorption during ethane recovery. When used in retrofitting for ethane recovery, only piping modification is required without the need for re-wheeling of the turbo-expander. TRAP can achieve over 90% ethane recovery with 99% propane recovery and is ideal for revamping existing NGL plants for ethane recovery.
Sub-cooled Absorption Reflux Process (SARP):
SARP is a sub-cooled lean absorption configuration that can avoid CO2 freezing during high ethane recovery. It is designed for feed gases with a high CO2 content and is capable of achieving ethane recovery in excess of 90% with propane recovery of more than 99%.
Enhanced Residue Gas Recycle (ERGR):
The process is designed to recover 99% propane during propane recovery and 95% ethane during ethane recovery using equipment of the propane recovery process. The design is switchable from propane recovery to ethane recovery by an enhanced by residue gas recycle configuration, which has been demonstrated suitable for variable nitrogen content feed gases.