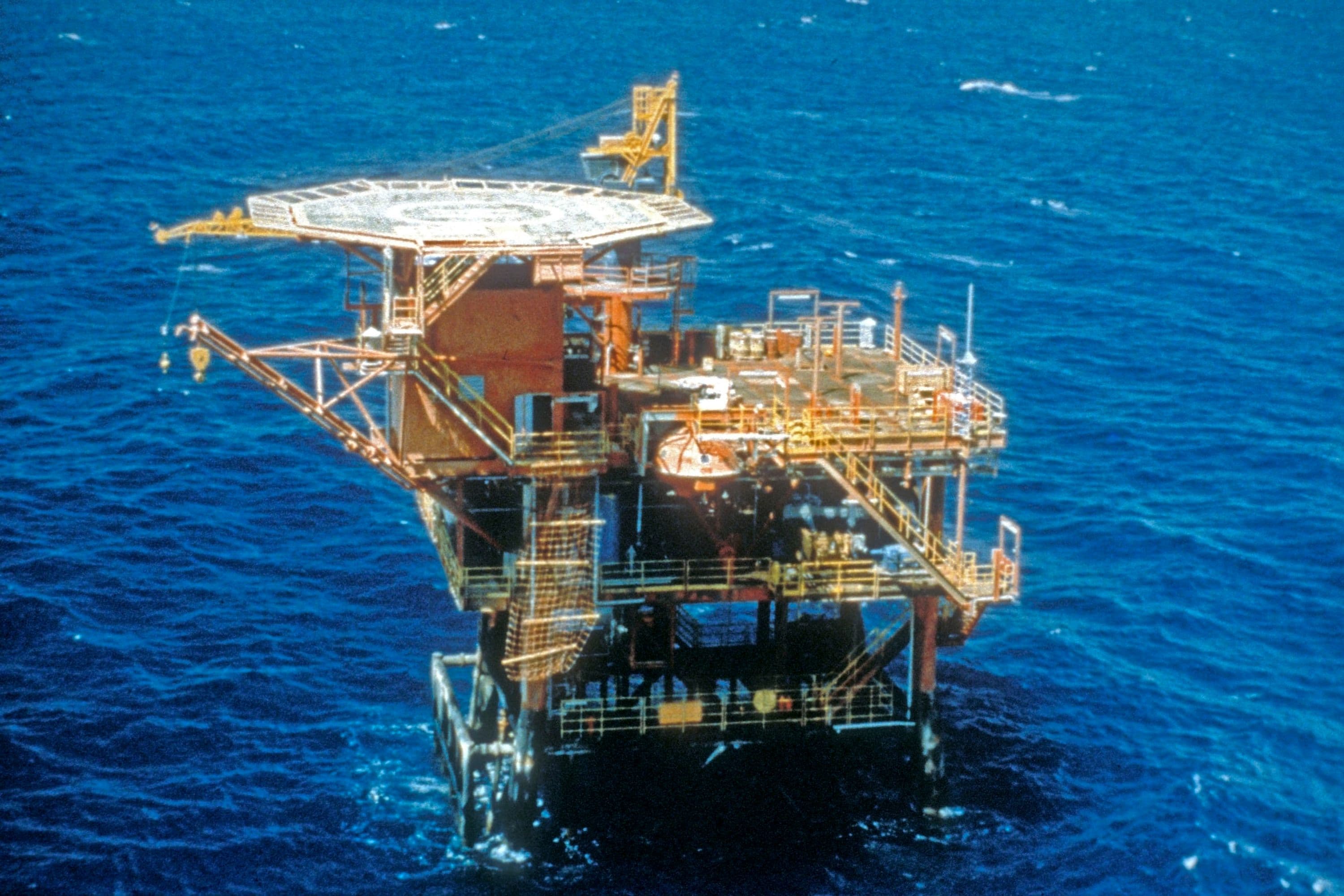
Suez Oil Ras Fanar Field Development - Project Management
Client: Suez Oil Company
Location: Gulf of Suez, Egypt
Business Segment: Energy Solutions
Industry: Fuels

Executive Summary
Fluor provided engineering, design, procurement services and construction assistance for the Ras Fanar Field offshore sour crude field development project located two miles offshore in the Gulf of Suez, Egypt. The project consisted of two production platforms (in 100-foot water depth), pipelines and power cables to shore, onshore separation equipment, a sweetened crude transfer pipeline and a gravity loading line to an offshore tanker loading berth
The project was complicated by the gaseous, sour crude, which would require special material and design considerations. Hydrogen sulfide and carbon dioxide concentrations of 10 mol % each needed close attention to corrosion-resistant material selection, chemical inhibition and strict safety measures.
Client's Challenge
The project was located on the west side of the Gulf of Suez and included two well-head platforms in approximately 100 feet of water, subsea pipelines, an onshore power plant, crude sweetening facilities and export facilities.
The four-pile, four-slot structures produced sour crude. The platforms are connected by an 8-inch diameter submarine flowline to the Egyptian General Petroleum Company (EGPC) treatment facilities on-shore. The line connected to EGPC's existing treating and storage facilities. The pipelines include pigging and slug catching facilities. The oil production rate will supply 15,000 barrels per day.
Fluor's Solution
Fluor provided the engineering, detailed design, materials and equipment procurement assistance, preparation of contracts for construction works and provision of specialist personnel as required during construction for the Suez Oil Company project.
We overlapped various engineering activities to keep on top of the schedule. We sent inquiries to vendors before detailed design was fully completed. For example, pipeline drawings, based on preliminary information, were used for pipe orders. Detail was later confirmed by hydrographic survey.
The Fluor team cut weeks off the schedule by negotiating a comprehensive, sole-source fabrication and construction contract. Materials for the two platform jackets were obtained from stock sources in Europe. Plate was fabricated into larger diameter jacket legs at the contractor's facilities in Dubai.
To further accelerate the schedule, we provided the first platform with only necessary facilities to meet "first oil ashore" requirements. The overall topsides equipment hookup closed followed the flowing for the first well.
Offshore power is supplied via a submarine electric cable loop that was linked to the local power grid. Temporary gas detection systems sniffed for any leakage of the 10% hydrogen sulfide crude before permanent equipment was in place. Seawater was initially pumped from a boat moored alongside the structure. Later pumps were installed on the platforms.
Conclusion
We used innovative approaches and our global procurement network to meet the demanding 12-month fast-track schedule to achieve first gas ashore. The first oil ashore was achieved by natural flow in January 1984, two months ahead of planned completion. Pumping facilities were also installed in the spring of 1984.