&w=3840&q=75)
GASCO NGL Extraction Plants
Client: GASCO
Location: Abu Dhabi, United Arab Emirates
Business Segment: Energy Solutions
Industries: FuelsEnergy Transition

Executive Summary
Fluor performed engineering, procurement and construction management for the Abu Dhabi Gas Industries Limited (GASCO) natural gas liquid (NGL) extraction plants at Bab and Asab in Abu Dhabi.
Client's Challenge
ADNOC and three other companies formed GASCO in 1977 as owner and operator of the new NGL facilities.
The NGL plants were required to be self-sufficient in utilities. This requirement necessitated the development of water wells and installation of water treating facilities. In addition, gas turbine powered generator sets were installed at each site to supply the necessary electrical power.
Auxiliary facilities were also built at each location including sewage treatment, flare stacks and burn pits, potable and fire water storage, diesel and gasoline storage, telecommunications system, fire and safety surveillance system, control building, electrical substations, fire station, inert gas generator, instrument air system and a mosque.
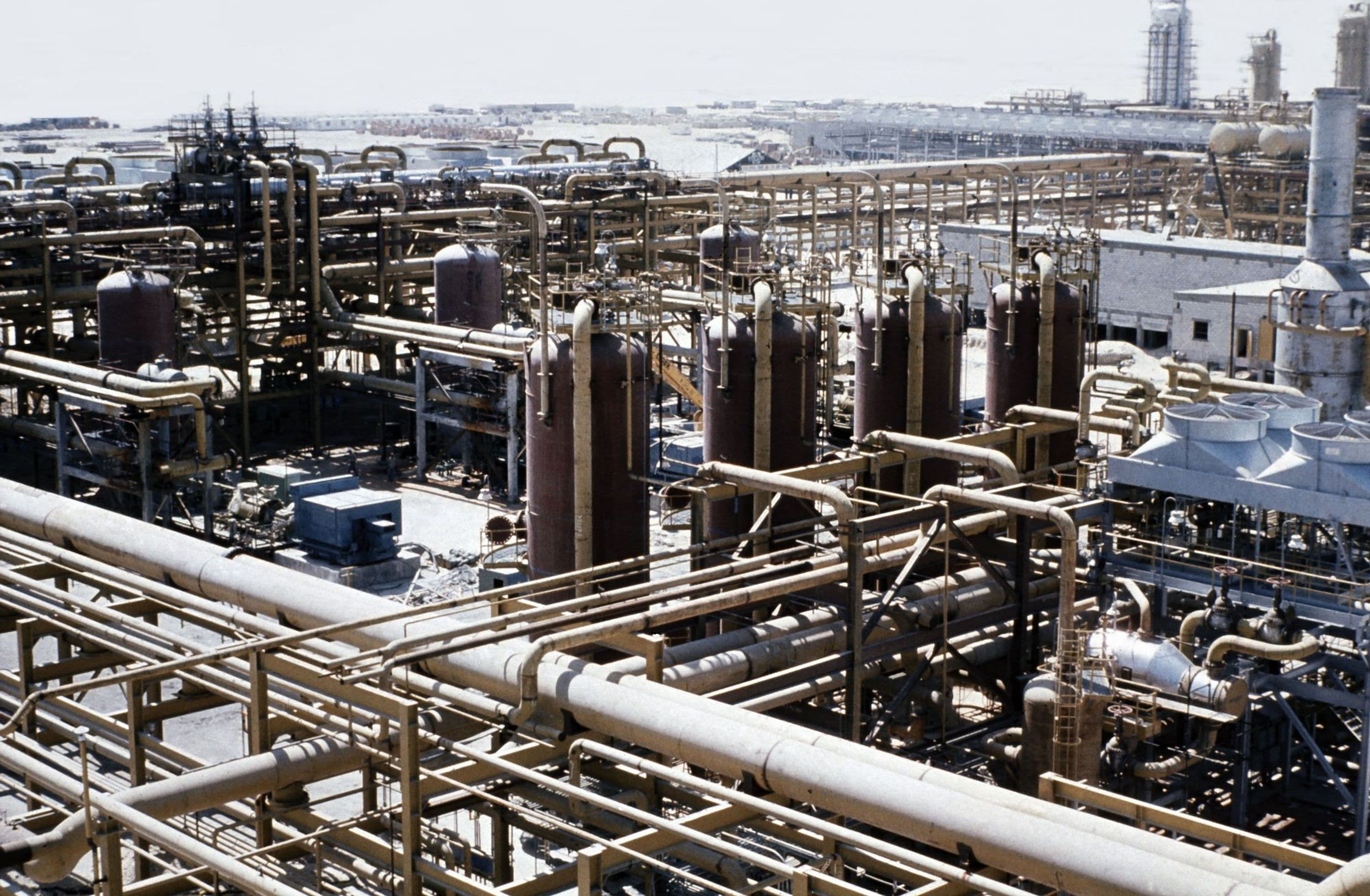
Fluor's Solution
Fluor performed engineering, procurement and construction management for GASCO's natural gas liquid (NGL) extraction plants at Bab and Asab in Abu Dhabi, which were rated at 130 MMSCFD and 350 MMSCFD.
The two plants were designed to recover a natural gas product from oil-associated gases that were being flared. The basic process consists of increasing gas pressure by motor and gas turbine driver compressors and lowering temperature using propane refrigeration and turbo-expansion. The resulting liquid product NGL is pumped via pipeline to Ruwais for fractionation into butane and propane products. The installation of water wells, water treating facilities, power generators and other auxiliary facilities was required at each location.
The client selected our Improved EconamineSM Process to achieve the desired results. Cost for direct field labor in the desert required prefabrication to the maximum extent. Therefore, major portions of the NGL plants were modularized and constructed in fabrication shops in the United Arab Emirates.
These plants are a portion of the Abu Dhabi gas project, which consisted of:
NGL extraction plants at Bab, Asab and Bu Hasa
Fractionation and storage facilities at Ruwais
NGL pipelines from the three NGL plants to fractionation at Ruwais
NGL product loading facility at Ruwais
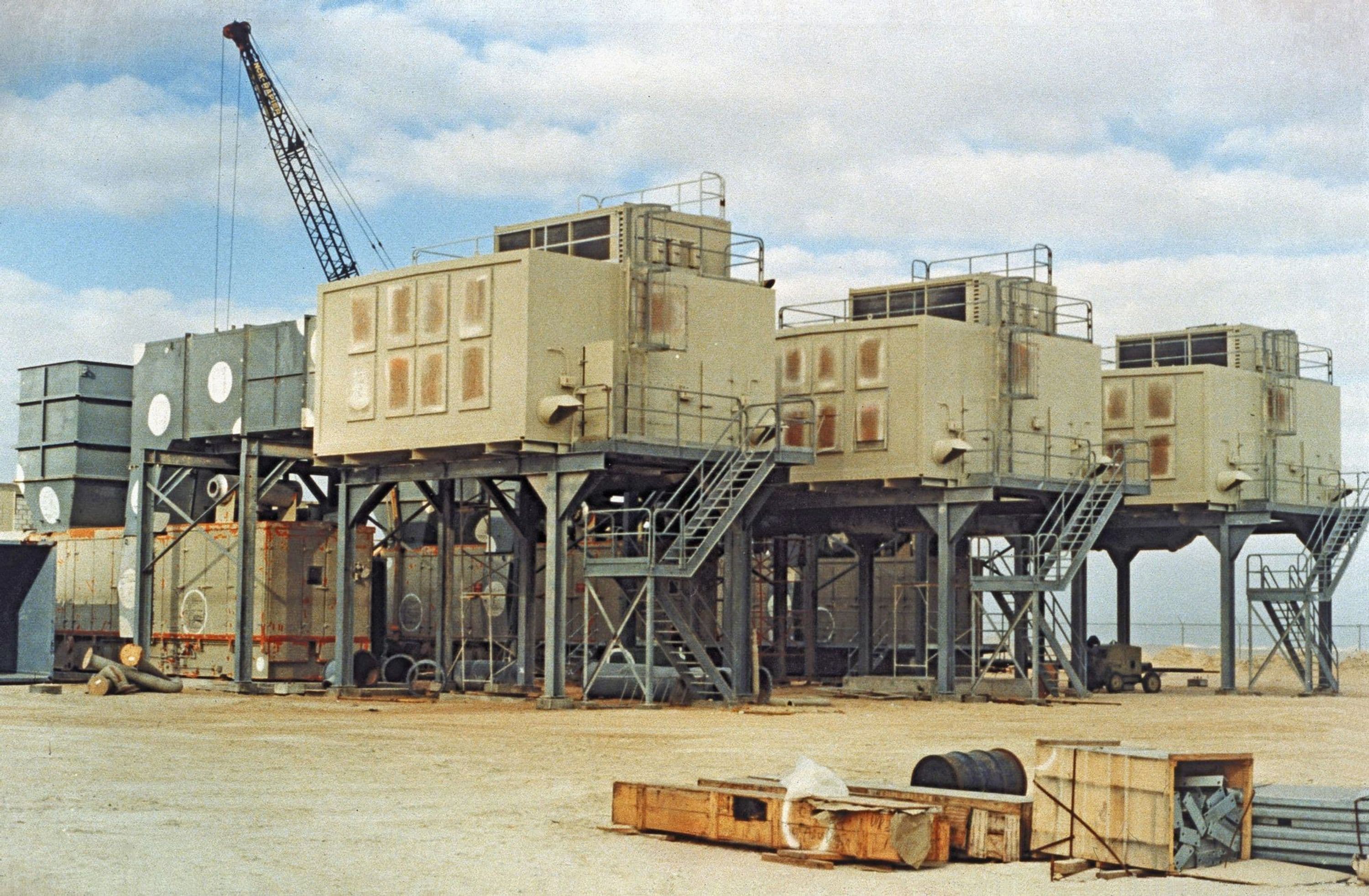
Conclusion
In addition to providing engineering, procurement and construction management services to GASCO, Fluor used our proprietary Improved Econamine process to remove H2S from the feed gas. We also had 80 modules fabricated in Abu Dhabi and shipped to the new facility via service boats and a specially designed, multi-tiered highway vehicle.
Each plant was designed to be self-sufficient in utilities; therefore, we designed and built fire and potable water systems and installed gas turbine generator sets to meet power needs.
Each plant also included a telecommunications system, fire and safety surveillance system and a mosque.
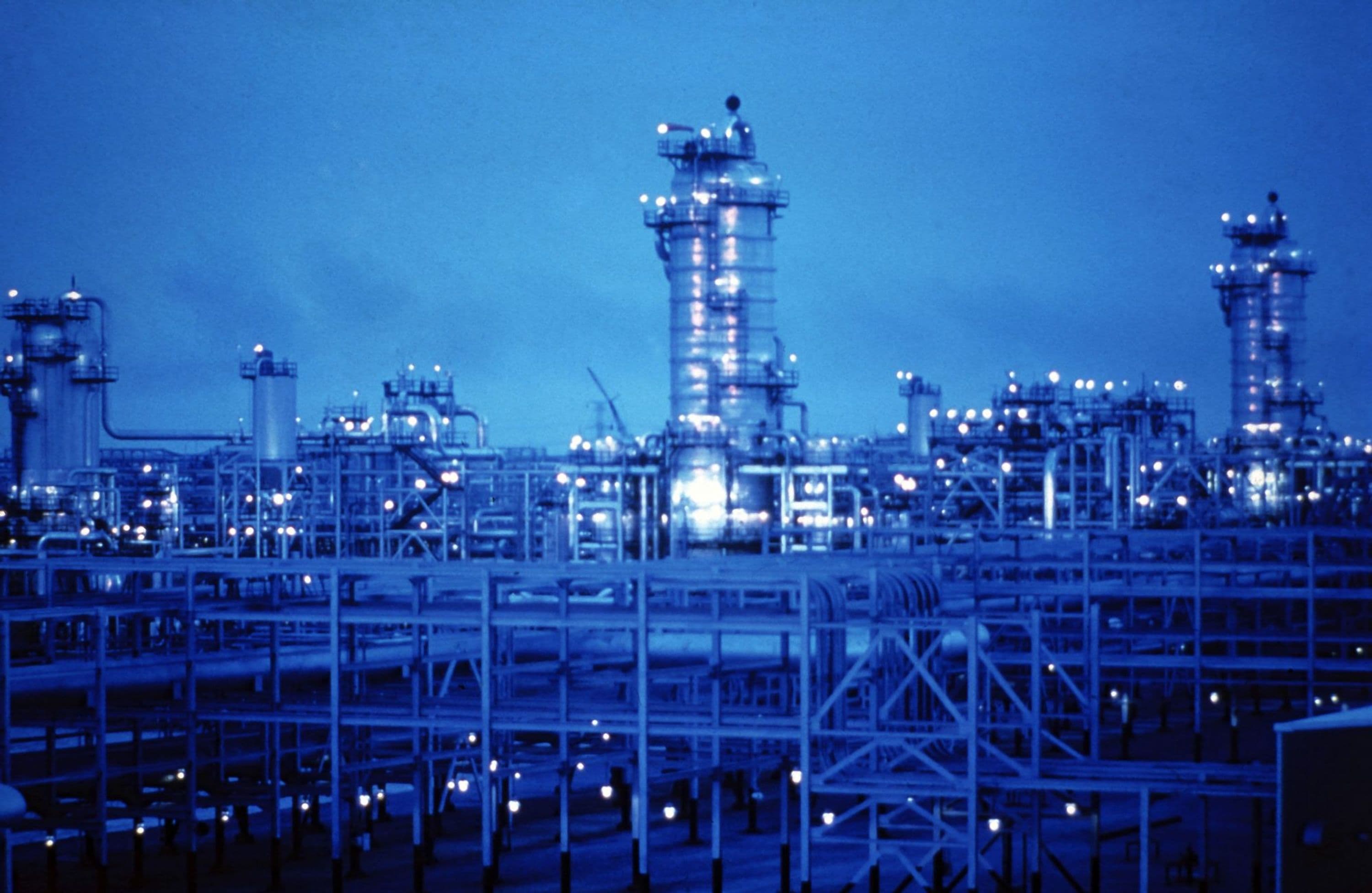