&w=3840&q=75)
Fort Hills Utilities Project - EPFC
Client: Fort Hills Energy L.P.
Location: Wood Buffalo, Alberta, Canada
Business Segment: Energy Solutions
Industry: Fuels
Services: FabricationEngineering and DesignProcurementConstruction

Executive Summary
Fort Hills Energy L.P. selected Fluor for its engineering design specification project, which then transitioned to the engineering, procurement, fabrication and construction (EPFC) phase. To support our integrated solutions approach, the partnership awarded a Fluor joint venture (JV) a contract for the assembly of modules for the Fort Hills Utilities project.
As structural steel and pipe spooling arrived onsite, the JV assembled the modules of varying types for the project, including pipe racks, structural assemblies, equipment modules and complex electrical and instrumentation assemblies. Instead of dispersing each module's components across multiple shipments, each skid included all the steel and bolts necessary to assemble one complete module (218 steel pieces). The project team and JV developed this innovative solution to ultimately improve schedule and reduce labor hours. The plant site was built to produce 180,000 bpd per calendar day of bitumen, a heavy and extremely viscous oil.
As of October 2016, all 358 modules had been fabricated and shipped to the site, where they would be set by Fluor's craft workforce. At the time, the site had achieved more than 2.8 million hours without a lost-time incident.
&w=3840&q=75)
Client's Challenge
The Fort Hills Project included the need for mining, ore preparation plant, extraction and tailings, froth treatment, utilities, electrical distribution, automation, third-party product handling, utilities block and infrastructure.
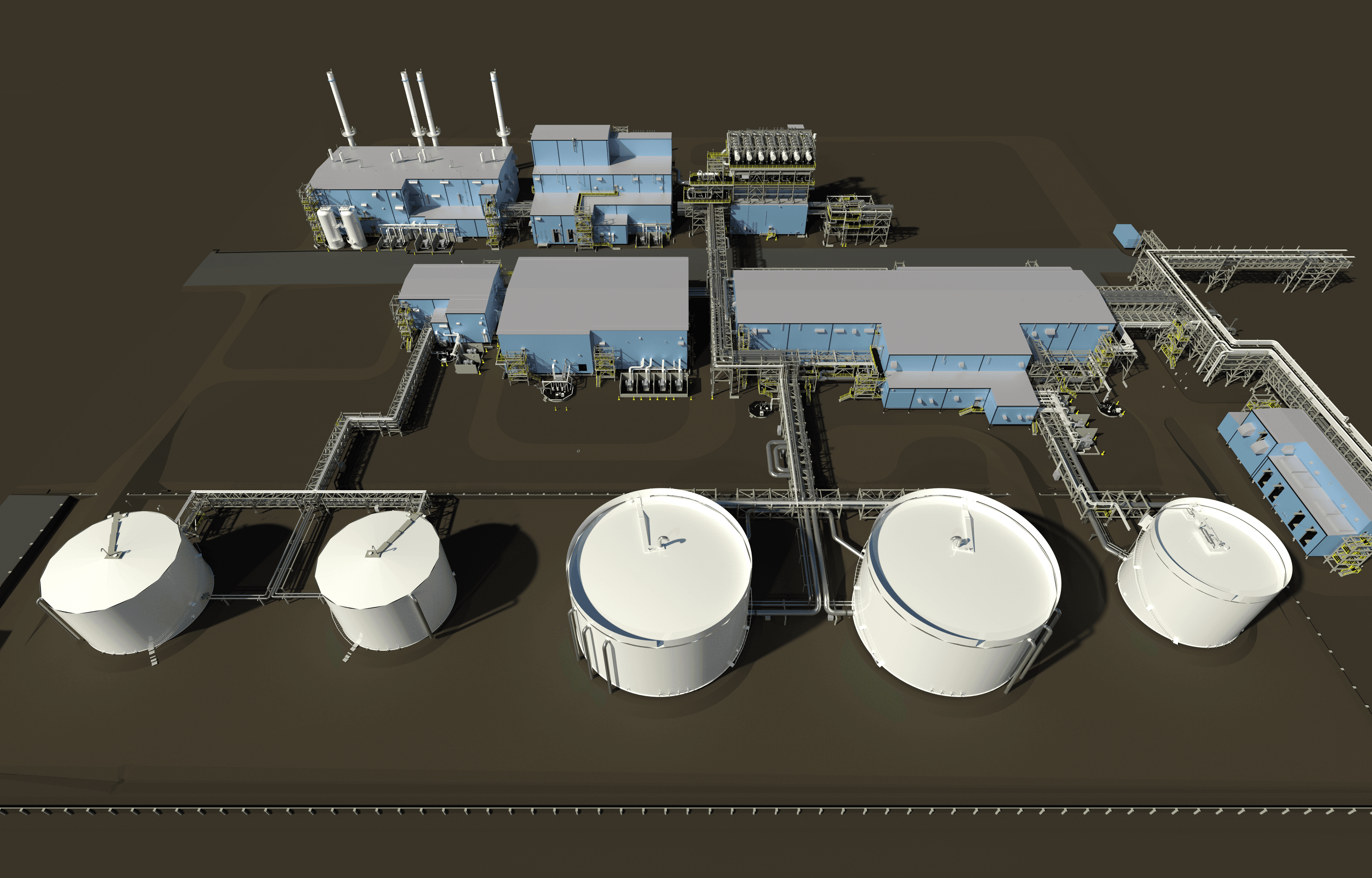
Fluor's Solution
Our scope included the utilities block, together with interface management. We were also responsible for the engineering design specification phase. Utilities structures, involved in producing the bitumen, were used for electrical distribution, automation and third-party product handling. We also carried out front-end engineering and design, engineering and procurement for these structures. The Fluor process team achieved reconfigurations and reissued process flow diagrams (PFDs). The project team also identified several opportunities to improve the internal rate of return for the project, including use of an innovative modular execution approach and an integrated EPFC solution with direct-hire construction and the use of a module assembly facility in Edmonton, Alberta, Canada. This was the first project to use the new modular execution approach in a distributed execution environment.
Additionally, the client mandated use of the AutoPLANT design platform, on which the Fluor project team excelled. This led the client to engage us in the audit process on other project areas. Excellent client relations resulted in sole source negotiation of the EPFC scope of the project for Fluor.
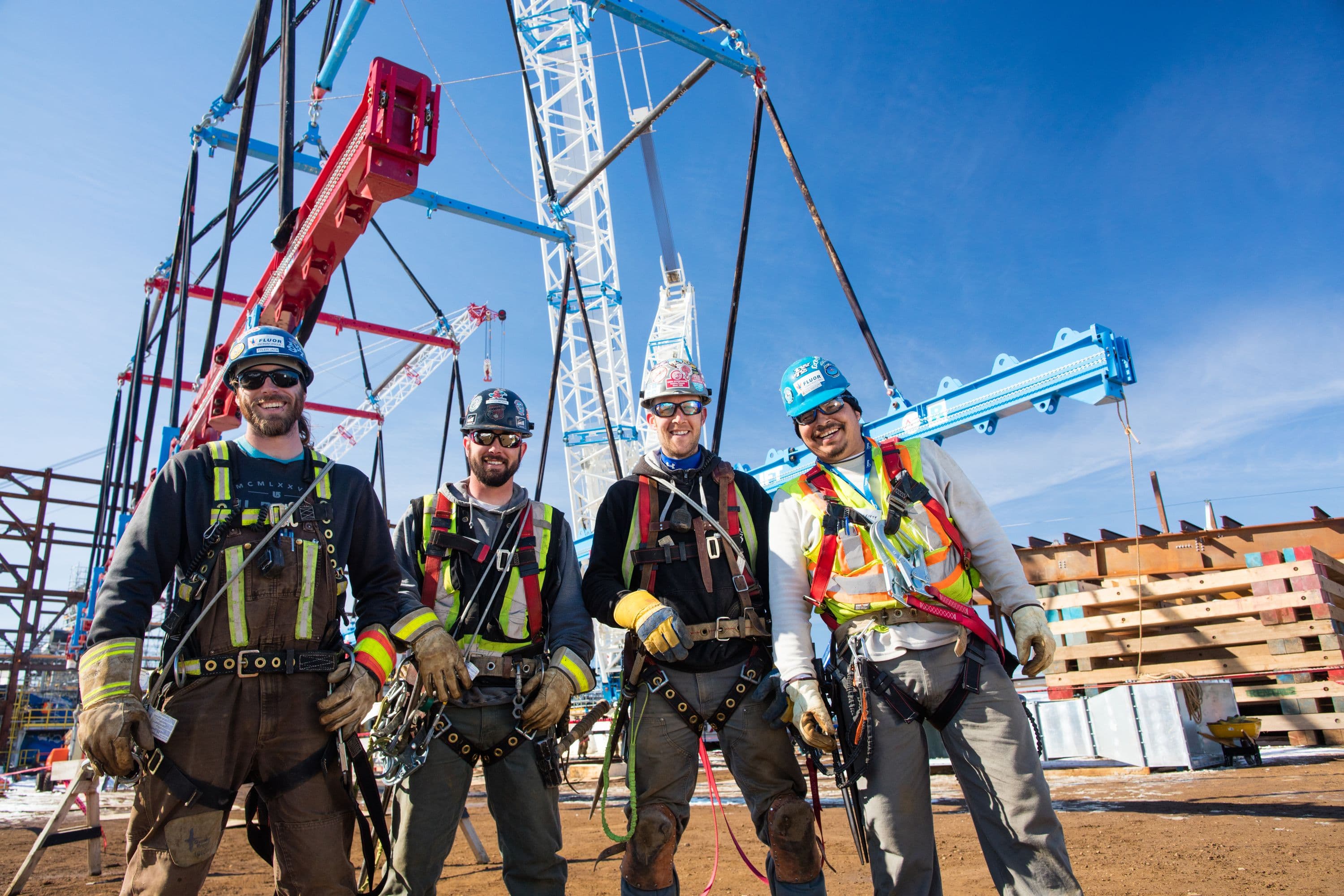
Conclusion
We applied an innovative modular execution approach in designing the utilities structure to ease delivery. As a result, the Fort Hills project was the winner of Fluor's Hugh Coble 2013 Award in the Home Office Services category.
&w=3840&q=75)