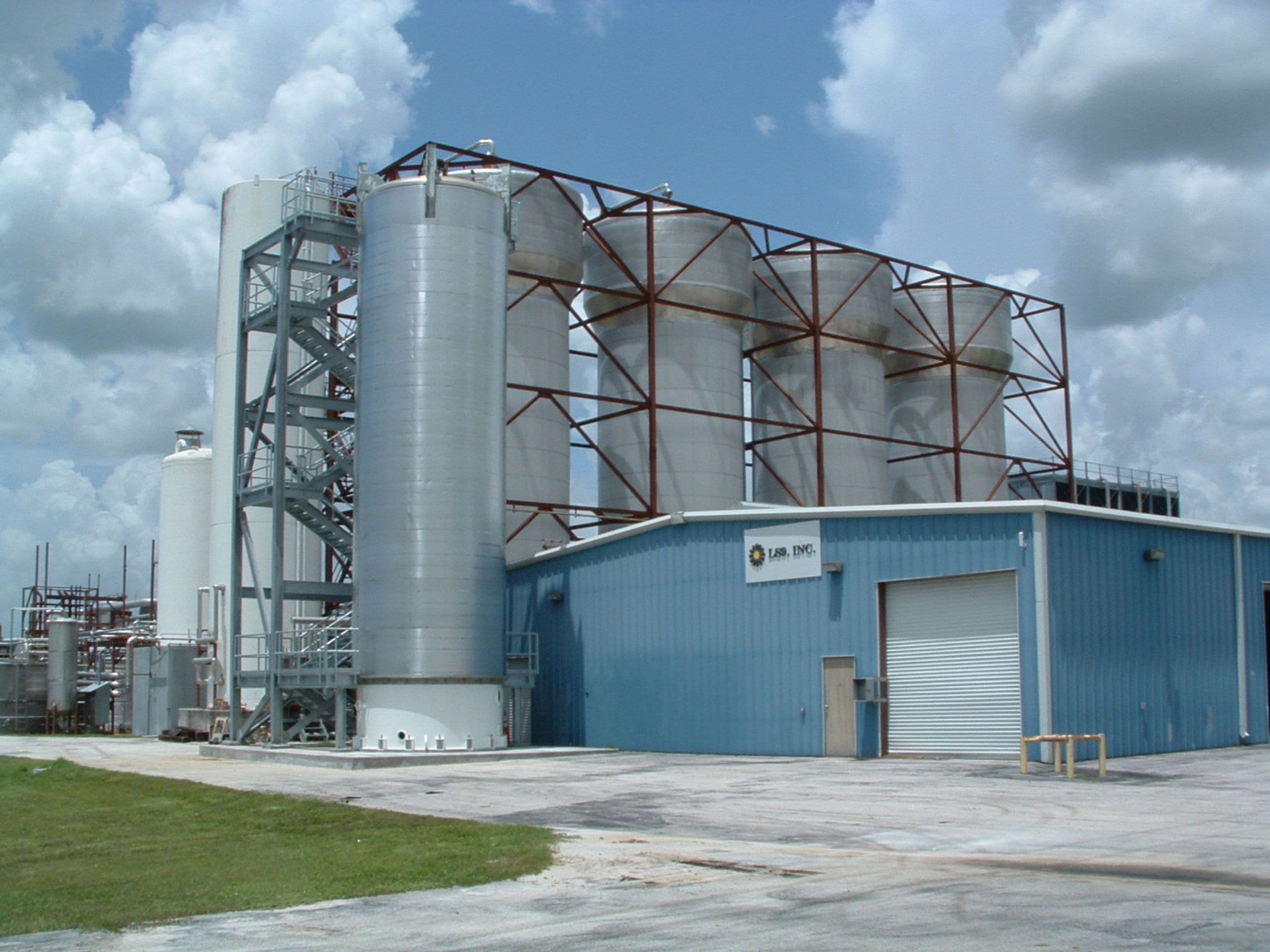
LS9 Biofuel Manufacturing Demonstration Plant - Engineering
Client: LS9, Inc.
Location: Okeechobee, FL, U.S.
Business Segments: Energy SolutionsUrban Solutions
Industries: InfrastructureFuels

Executive Summary
Fluor was selected by LS9, Inc. to conduct a study and perform engineering to retrofit an existing facility to accommodate biofuel production on an industrial scale. LS9, a privately held industrial biotechnology company, developed a technology to convert plant-based sugars into ultraclean renewable biofuels.
Client's Challenge
LS9 was developing patent-pending fuels and sustainable chemicals made with the power of synthetic biology. The company genetically engineered microorganisms used in proprietary fermentation processes to produce renewable fuels and sustainable chemicals.
One of the first processes developed by LS9 was a fermentation-based process for making UltraClean Diesel using sugars. The technology was demonstrated successfully at bench- and pilot-scale. In order to attract investment for commercial operations, proof at an industrial scale was needed.
The company's funds and resources for this effort were limited. Using information developed by Fluor in a conceptual study, the company identified an existing yeast fermentation facility in Okeechobee, Florida that closely met its requirements. The foreclosed property was purchased for an attractive price.
The challenge for LS9 was to quickly and cost-effectively retrofit the abandoned facility to accommodate its biofuel processes.
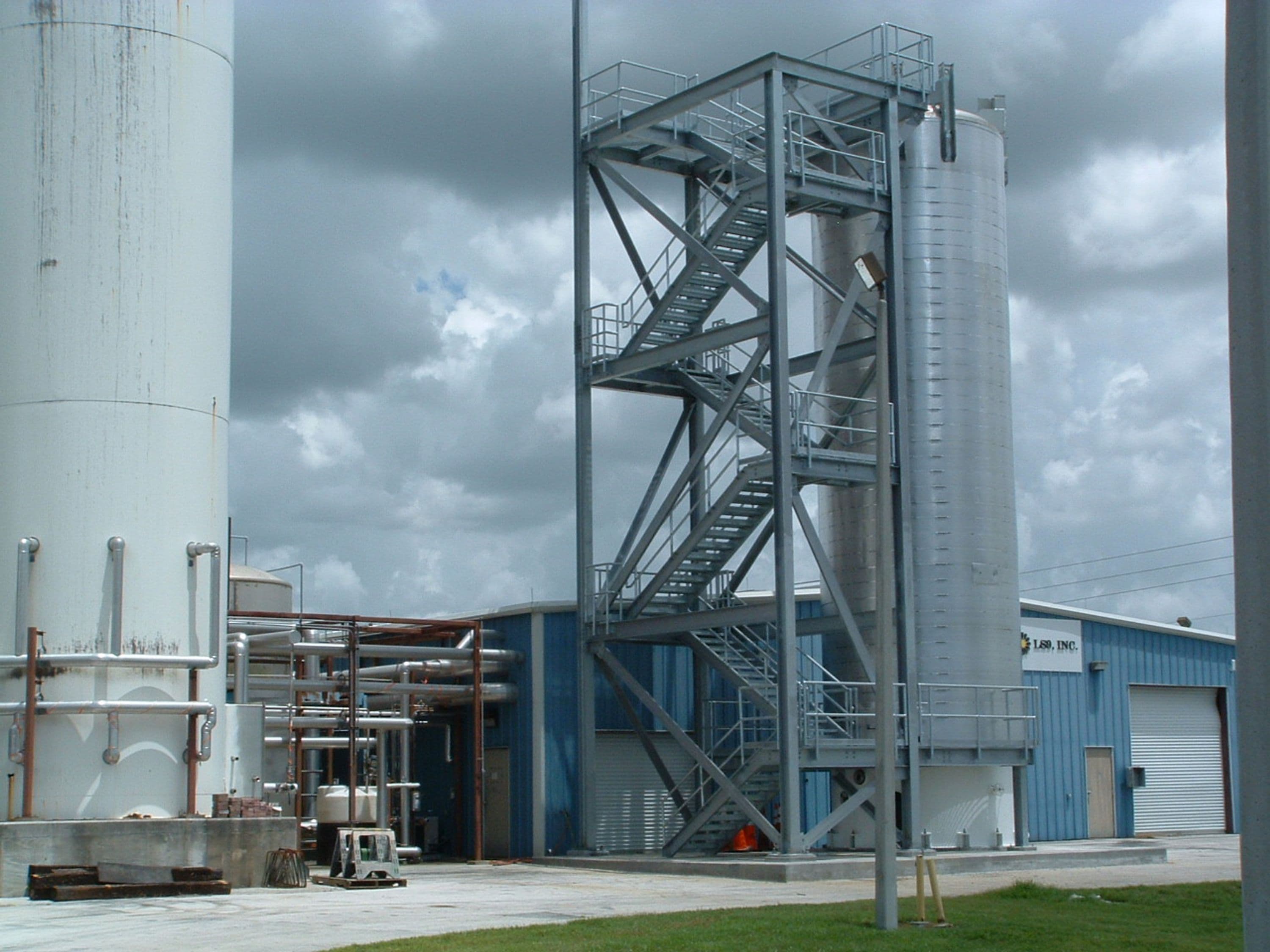
Fluor's Solution
The Fluor engineering team used knowledge from our conceptual study for a greenfield plant to evaluate a retrofit of the Okeechobee facility. After determining how to make best use of the existing equipment and systems, we developed a plan to upgrade the facility in two phases. These supported scale-up of the LS9 process in parallel with engineering of the larger-scale retrofit.
Phase 1 was an upgrade of the existing seed fermenters to accommodate the LS9 proprietary organisms and to allow small-scale separation of products with portable equipment. The upgrade was approximately a 6X scale-up of the LS9 pilot facility in South San Francisco. Phase 2 included installation of a 35,000-gallon fermenter and retrofit of the existing plant to full downstream operations for production of UltraClean Diesel.
We repurposed and retrofitted the existing equipment and controls onsite and purchased used equipment where possible to keep project costs down while ensuring a functional demonstration facility. The existing automation system was utilized as much as possible and augmented with new systems as needed.
Our engineering was completed in less than six months. At the same time, work continued on development of LS9 processes in response to LS9's ongoing modifications.
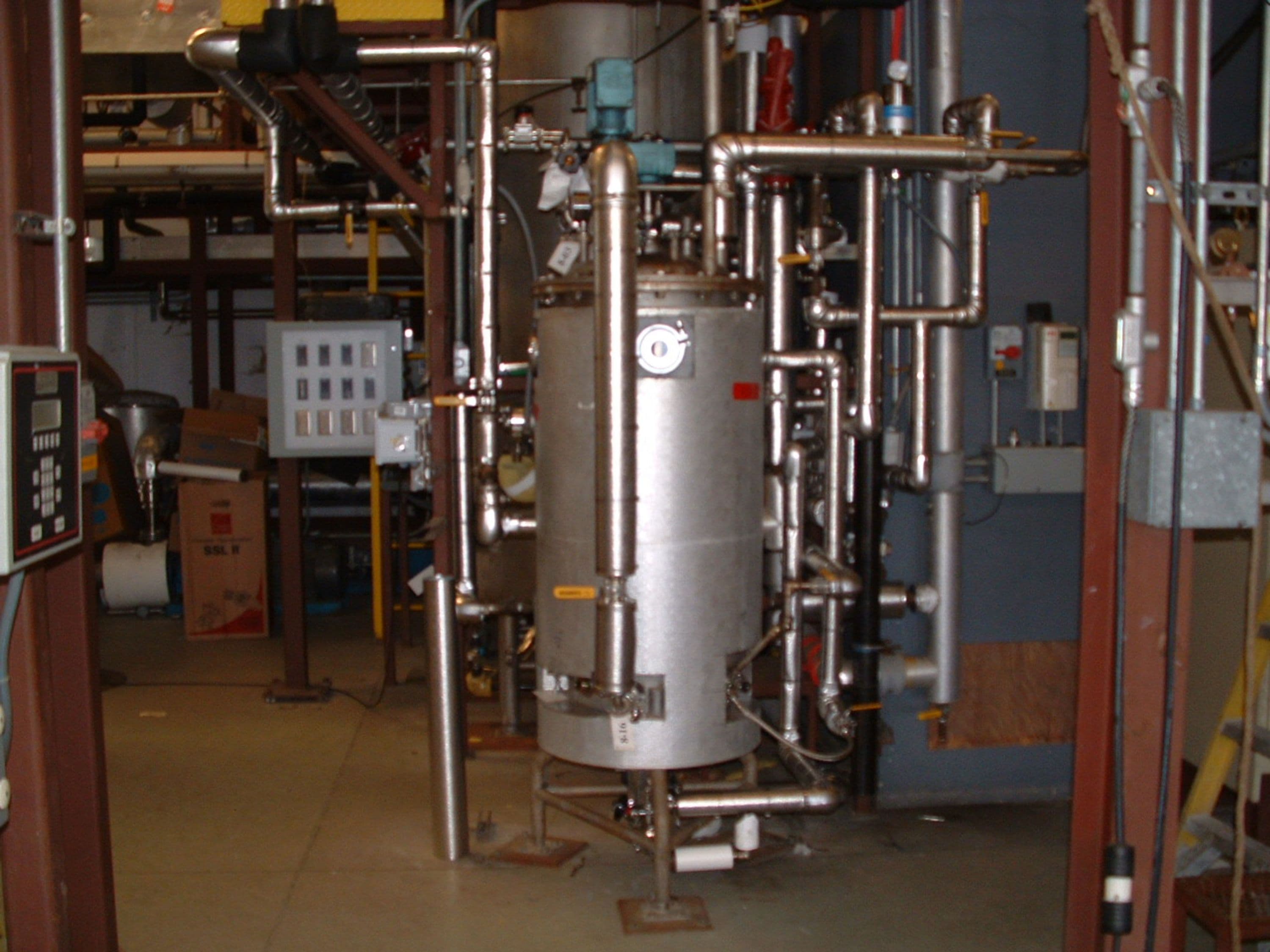
Conclusion
Fluor's knowledge of client needs and team expertise allowed engineering to be completed in a very short time, in line with LS9's key goals regarding cost and schedule. The team was flexible in working with the client's process development group.
In 2011, LS9 announced that it had successfully scaled its technology to the 20,000 liter scale. The company completed its first production run of fatty alcohols at the 135,000 liter scale in 2012.
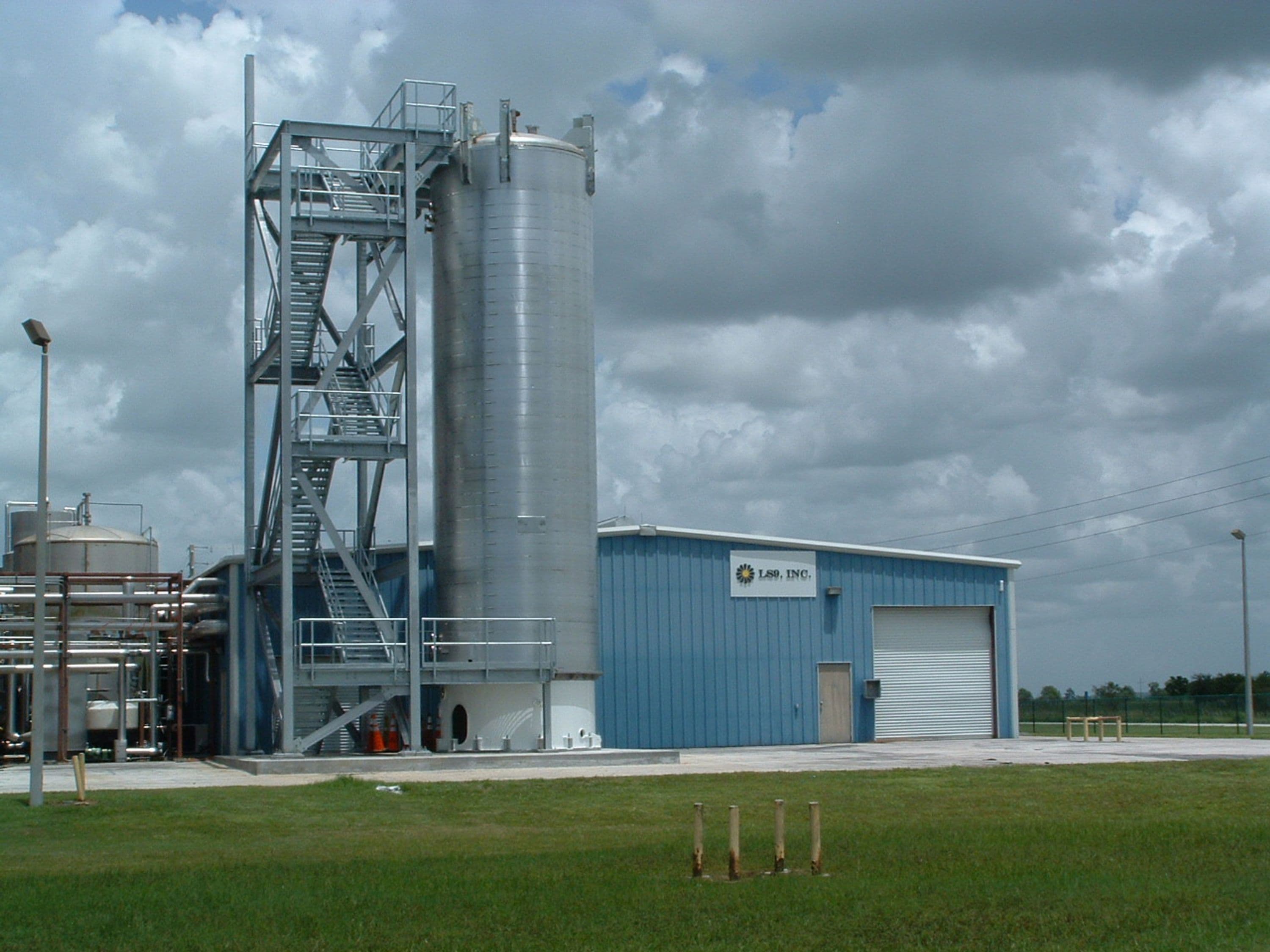