&w=3840&q=75)
Pharma Water Systems Require Expert Design for Sustainability
Pharma Water Systems Require Expert Design for Sustainability
By Katarzyna Grudnik, Senior Process/Specialty Engineer, Fluor, Advanced Technologies & Life Sciences
Sustainability by design is a key factor in achieving low-cost, long-term solutions in the pharmaceutical industry. Modern pharmaceutical facilities are designed with sustainability at the heart of day-to-day operations, with features such as contemporary HVAC design, isolators and other modern equipment. These features have reduced the energy demands of clean spaces by reducing the volume of clean space required.
Fluor has been a trusted partner to clients in the life sciences industry for more than four decades, delivering front-end design, engineering, commissioning and qualification services.
Fluor provides tailor-made solutions to meet client needs. Within the process team and Global Water Group of specialists, we have the experience to support clients in water and water treatment-related matters from concept to implementation.
In our work around the world, we are seeing sustainability initiatives from investment in renewables to low-carbon inhalers to net-zero buildings. Subsequently, there is an increasing focus on evaluating and reviewing the energy and water-intensive operations across different industries, including pharmaceutical manufacturing on our projects in Denmark and the United States. Sustainable design and engineering involve minimizing lasting environmental impacts. From a design perspective, this involves using environmentally friendly building materials and minimizing the use of non-renewable resources.
In pharmaceutical water treatment systems, sustainable design is inextricably linked to water conservation, water reuse and wastewater minimization. Designers, owners and operators of these systems, already facing increasing challenges in an increasingly competitive business environment, are aware of the synergy between caring for the environment and efficient operation. Companies are adopting policies that aim to simultaneously run a lean operation and promote a culture of social and environmental responsibility.
Greater Sustainable Pharma Water Systems
Water is essential to produce pharmaceutical ingredients, intermediates and final products. Accordingly, the quality requirements are particularly high.
Clean water for pharma manufacturing is a key utility in the manufacturing process and would be a logical target for green design due to the limited availability of source water and concerns about conservation and contamination, as well as inefficiencies and production costs. As water use and wastewater costs increase and regulations on drinking water quality become more stringent, water conservation techniques offer a promising solution to minimizing utility costs. This covers pharma-grade water generation, water storage and distribution and solutions that help reduce water consumption. In the pharmaceutical industry, the production of purified water, high-purity water, water for injection and clean steam in accordance with international pharmaceutical standards is considered a priority that must also meet environmental regulations. This industry is water-intensive, and production processes are designed to be resilient and ensure patient safety. To ensure the removal of any contamination and avoid cross-contamination, extensive cleaning processes are used, requiring significant treated and clean water.
Reducing and reusing water consumption is becoming an increasingly important part of pharmaceutical manufacturers’ strategic sustainability plans. There are various methods of reducing water consumption in the pharmaceutical industry. These opportunities can be divided into three categories:
The efficiency of making clean water
The efficiency of using clean water
The efficiency of recycling used water
This article discusses only the first category: the efficiency of making clean water.
Sustainability in Pharma Clean Water Production
Purified water, used either as a utility or an ingredient in pharmaceutical processes, is one of the most expensive systems to purchase, operate and maintain in a pharmaceutical facility. Water treatment technologies often require the use of chemicals, energy and time to maintain the high degree of reliability required by most stakeholders. Additionally, techniques such as filtration and distillation, which involve purification by dilution of process streams, produce concentrated streams as by-products of the operation. Traditional reverse osmosis (RO) systems have historically been known to be inefficient as they may send around 25 percent of incoming water to the drain. Moreover, common applications of pharmaceutical RO often rely on a significant number of pre-treatment operations such as water softening, dechlorination and suspended solids reduction to operate effectively.
There are many opportunities to save water and improve the efficiency of high-purity water systems. Better process monitoring can lead to reduced maintenance. Examples include backwashing media filters based on pressure difference across the filter rather than time as well as regeneration of water softeners and ion exchange units based on wastewater quality.
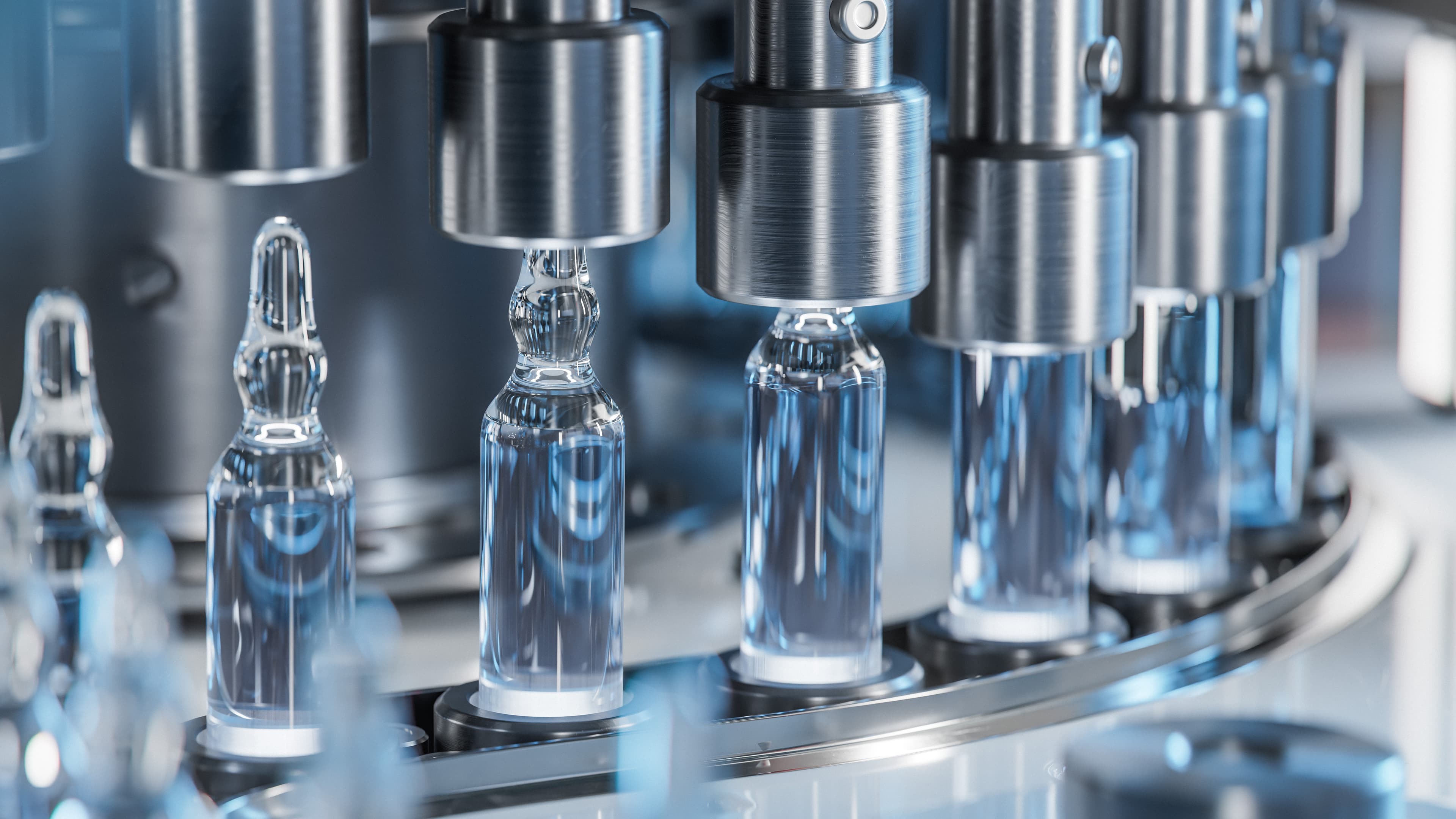
Designing and operating a pharmaceutical water system with feedwater recovery levels as low as 75 percent is unacceptable by today’s environmental and business standards. However, there are many opportunities to improve the operational efficiency of both new and existing systems, which are described as follows:
High-recovery RO systems can help minimize wastewater generation. Methods to improve RO recovery include high-quality pretreatment, novel membrane technologies and sacrificial membrane components, brine recovery systems to recover leachate water and systems that reuse the rejected water from RO and electrodeionization systems. These streams are often already softened, dechlorinated and filtered, making their reuse suitable for most boiler feedwater or cooling tower make-up. Additional non-potable uses include water supplying toilets and irrigation.
While all these options provide valuable benefits, the best solution for designing a purified water loop involves integrating advanced technologies and sustainable practices to ensure efficiency and minimal environmental impact using multi-stage filtration, including RO and ultraviolet sterilization, to ensure high-water purity. Variable frequency drives can adjust pump speed based on demand, reducing energy consumption.
Further, there are several approaches to improving the energy demand of existing technologies, such as:
Reduction of heat losses of distillation plants
Recovery of heat from wastewaters in distillation plants
Adjustment of the required water temperature at the point of use
Increased overall yield of RO plants
Reduction of the amount of wastewater that needs treatment
Introduction of new technologies
Summary
High-quality water systems – including water quality, production, storage and distribution – are an integral part of pharmaceutical manufacturing. As the industry continues to expand, the importance of sustainable water and energy use will be crucial to comply with global environmental goals. Pharmaceutical companies can contribute to a greener future by leveraging energy-efficient technologies, using renewable energy sources and promoting sustainability throughout the supply chain.
Making existing high-purity water systems more sustainable or designing new purified water systems requires expert technical knowledge to implement cost-efficient solutions to achieve the same benefits. For example, single-use technology replacing backwashing or regenerative processes should be assessed based on the overall environmental impact. Water consumption or generation processes should always be one of the areas considered for sustainable design and operation of systems.
As pharmaceutical companies work toward more sustainable practices for their water systems, it is important to critically examine alternatives and associated costs. Fluor is proud to support our clients in reviewing cost-effective, energy-efficient, sustainable, yet fully compliant and robust systems. Our teams offer expert engineering, procurement and construction management solutions that enable pharmaceutical manufacturers to efficiently and cost‑effectively select sustainable designs.
&w=3840&q=75)
Katarzyna Grudnik is based in Fluor’s office in Gliwice, Poland. She is a process engineer with nearly 20 years of experience in process engineering design for battery, life science, pharmaceutical, coal, biomass, refinery, petrochemical and chemical plants.